خط تولید دستگاه قالب سازی پلاستیک
راه اندازی خط تولید دستگاه قالب سازی پلاستیک بسیار سود آور است چون با توجه به شیوه زندگی جدید صنعت پلاستیک به یکی از مهم ترین و پر کاربرد ترین صنایع تبدیل شده است به دلیل استفاده از محصولات پلاستیکی در صنایع مختلف می توان این صنعت را پایه بسیاری از صنایع دانست.
قطعات و محصولات پلاستیکی که روزانه به تنوع آن ها اضافه میشود کاربرد بسیار زیادی در زندگی روزمره و صنعت دارد .قطعا تاکنون به نحوه تولید این محصولات فکر کردهاید…
تزریق پلاستیک یکی از روشهای تولد است که به طور گسترده و وسیعی در ساخت و شکل دهی قطعات مختلف از ساخت اسباب بازی تا قسمت های پلاستیکی بدنه خودرو، بطریهای آب و انواع موبایل کاربرد دارد.
تزریق پلاستیک یک تکنولوژی ساخت برای تولید انبوه قطعات پلاستیکی یکسان با خطای پایین است. برای راه اندازی خط تزریق پلاستیک نیاز به دستگاه تزریق پلاستیک و دستگاه قالب سازی پلاستیک است.
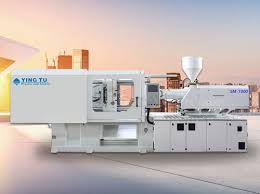
راه اندازی خط تولید دستگاه قالب سازی پلاستیک:
اگر قصد ورود به صنعت تولید قطعات پلاستیکی و یا ایدهی راه اندازی یک خط تولید تزریق پلاستیک را دارید، مواردی را باید برای راه اندازی خط تولید تزریق پلاستیک در نظر بگیرید. برای تحلیل اولیه و بررسی میتوان از مشاوره راه اندازی خط تولید کمک گرفت.
چه مواردی را باید برای راه اندازی این خط تولید در نظر گرفته شود؟ مواردی که برای راه اندازی این خط تولید تزریق باید در نظر گرفته شود شامل موارد زیر است:
- انتخاب محصول:
در ابتدا برای راه اندازی خط تولید باید محصول یا محصولات مشخصی را در نظر گرفته و بازار هدف خود را شناسایی کنید. بر اساس تجربه محصولاتی که تاکنون در داخل تولید نشده اند و یا محصولاتی که تقاضای زیادی در بازار برایشان وجود دارد سودآوری بیشتری دارند، بنابراین انتخاب بهتری به شمار میآیند.
- تحلیل محصول:
در گام دوم روش تولید مناسب را انتخاب کنید و به این منظور لازم است شکل هندسی، تیراژ تولید و جنس محصول به دقت تحلیل شود. برخی از ساختارهای هندسی مثل دهانهی باریک تر از بدنه یا شیب منفی محصول با روش تزریق پلاستیک قابل تولید نیست.
در این شرایط باید سایر روشهای تولید پلاستیک مانند روش بادی یا بادی-تزریقی را انتخاب کنید. در صورتی که تیراژ تولید محصول بسیار پایین است و یا نمونه سازی مورد نظر است، خرید ماشین آلات و حتی ساخت قالب توجیه اقتصادی ندارد، در چنین شرایطی روش پرینت 3 بعدی توصیه میشود. جنس محصول نیز در انتخاب روش تولید موثر است.
- تحلیل مواد اولیه:
در گام سوم مواردی از قبیل رنگ، افزودنی، و نوع ماده اولیه باید مورد بررسی قرار گیرند. همچنین تامین کنندگان مواد مورد باید شناسایی شود و استعلام قیمت انجام شود.
در صورتی که مواد اولیه مورد نیاز برای تولید محصول در داخل کشور موجود نباشد، باید نحوه ی واردات و تامین مواد اولیه نیز درنظر گرفته شود. در این مرحله لازم است برآورد دقیقی از قیمت مواد اولیه و میزان مصرف آن صورت پذیرد تا برای تخمین قیمت تمام شده مورد استفاده قرار گیرد.
- فضای کارخانه:
فضای واحد تولیدی باد کافی برای استقرار ماشین آلات و لوازم جانبی، تردد افراد انبار و حمل بار را داشته باشد. حداقل ارتفاع توصیه شده برای کارخانه تزریق پلاستیک 4.5 متر است و در صورت استفاده از جرثقیل سقفی، حداقل ارتفاع 5.5 متر مورد نیاز است.
به دلیل وزن قابل توجه ماشین آلات تزریق پلاستیک، بتن ریزی بهترین گزینه برای کف سازی کارخانه به شمار می رود. علاوه بر موارد یاد شده، سیستم تهویهی مناسب نیز به عنوان یکی از ضروریات فضای کارخانه تزریق پلاستیک است.
- مشاوره و ساخت قالب:
قالب تزریق پلاستیک جزء ضروری برای تولید قطعه محسوب شده و انتخاب سایز و نوع دستگاه تزریق پلاستیک مستقیما به آن بستگی دارد. پیش از خرید دستگاه باید مواردی مانند ابعاد قالب، نوع راهگاه، بازشو مورد نیاز، شات تزریق و نیروی گیره مورد نیاز در با یک مشورت قالبساز حرفه ای مشخص شوند. هزینه ساخت قالب نیز باید مورد توجه قرار گرفته و در محاسبه قیمت تمام شده قطعه مورد استفاده قرار گیرد.
- ماشین آلات:
گام بعدی پیش بینی و استعلام قیمت ماشین آلاتی است که در خط تولید تزریق پلاستیک باید باشند. رایج ترین قطعات و ماشین آلات در کارخانههای تزریق پلاستیک عبارتند از:
- دستگاه تزریق پلاستیک.
- کنترل کننده قالب.
- چیلر.
- گازگیر.
- موادکش.
- آسیاب.
- مخلوط کننده مواد (میکسر).
- تجهیزات اتوماسیون.
بر اساس نوع محصول تولیدی و نرخ تولید مورد انتظار، ممکن است تمام و یا بخشی از تجهیزات فوق را نیاز داشته باشید، برای تخمین دقیق قیمت ت باید تجهیزات مورد نیاز تعیین شده و قیمت هر یک استعلام شود.
- تاسیسات:
پس از تعیین ماشین آلات و تجهیزات، مقدار جریان برق مورد نیاز بر حسب آمپر مشخص میشود. دستگاههای تزریق پلاستیک با برق صنعتی 3 فاز کار می کنند و عموما به جریان بالا احتیاج دارند. علاوه بر برق، آب خنک نیز یکی از ضروریات راه اندازی خط تولید تزریق پلاستیک است.
آب خنک را میتوان از طریق چیلر، برج خنک کن، چاه آب یا … تامین کرد، البته استفاده اختصاصی از چیلر صنعتی هواخنک برای هر دستگاه، گزینهی قابل توصیه است. برای تولید برخی از قطعات خاص، هوای فشرده نیز مورد نیاز است که در این صورت باید تجهیزات و تاسیسات مورد نیاز برای تامین آن پیش بینی شده و در قیمت تمام شده لحاظ شود.
محصولات قابل تولید در خط تولید دستگاه قالب سازی پلاستیک:
عمده کاربرد این خط تولید در ایران به تولید انواع سبد میوه، گلدان، سطل، ظروف آشپزخانه پلاستیکی، قطعات خودرو و … اختصاص دارد.
مهم ترین محصولات شامل:
- سبد میوه.
- گلدان پلاستیکی.
- ظروف IML.
- جار.
- پریفرم.
- سپر و قطعات کوچک و بزرگ خودرو.
- میز و صندلی.
هزینه راه اندازی خط تولید دستگاه قالب سازی پلاستیک:
برای محاسبه راه اندازی خط تزریق پلاستیک فاکتورهای زیادی وجود دارد.
از جمله این فاکتورها در نظر گرفتن هزینهی مواد اولیه، هزینهی ماشین کاری و مدت زمانی است که باید صرف عملیات ساخت شود. منظور از ماشین کاری هزینهای است که قرار است صرف ساخت قالب شود.
هر قالب برای جسم خاصی با ابعاد و اشکال مختلفی تولید میشود. هزینهای که صرف تولید قالب میشود با تعداد قطعههایی که قرار است تولید شود رابطهی عکس دارد. با توجه به موارد گفته شده میتوان فرمولی به شکل زیر ارائه داد:
هزینه نهایی راه اندازی خط تولید تزریق پلاستیک = هزینه مواد اولیه + هزینه ساخت قالب تزریق پلاستیک + هزینه زمان اختصاص داده شده به کار با توجه به نیروی انسانی یا ماشینی +هزینه خرید دستگاه + هزینه فضای کارگاه
چرا راه اندازی خط تولید تزریق پلاستیک خوب است؟
اول این که کشور ما، در این حوزه، به خاطر داشتن منابع سرشار نفت و البته تولید انواع مواد اولیه با گسترش پتروشیمی ها دارای مزیت نسبی است. و دوم هم این که محصولات بسیار متنوعی را می توان با در اختیار داشتن این مواد اولیه و البته دستگاه مربوطه ساخت؛ از انواع سبد میوه، ظروف پلاستیکی خانه و آشپزخانه، جالباسی، صندلی تا اسباب بازی ها و قطعات لوازم خودرو. این تنوع باعث ایجاد انبوهی از ایده ها برای کارآفرینان می شود که می تواند هم ناب و هم جذاب باشد.
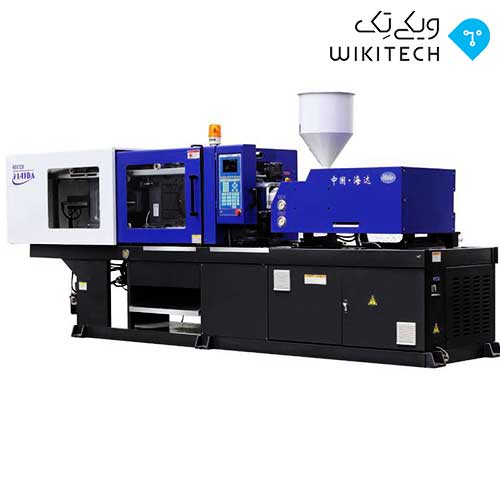
چرا روش تزریق پلاستیک؟
اگر این مطلب را میخوانید، احتمالاً در مورد قالبگیری تزریق پلاستیک یکی دو نکته اصلی را میدانید. دلایل زیادی وجود دارد که چرا روند قالبگیری تزریقی در زمینه تولید پلاستیک بسیار محبوب است. رایجترین دلیل این است که این دستگاه بهترین وسیله برای تولید مقادیر عظیم و یکسان قطعات پلاستیکی است. انواع مختلفی از دستگاهها قالب سازی وجود دارد، که انتخاب این دستگاه بسته به آنچه که شما تولید میکنید و همچنین دستگاه چگونه بر محصول تأثیر می گذارد، وابسته است.
فرآیند دستگاه قالب سازی پلاستیک:
قالبگیری تزریقی کاربردیترین فرآیند تولید برای ساخت انواع قطعات پلاستیکی است. طیف گسترده ای از محصولات با استفاده از این روش تولید میشوند که از نظر اندازه، پیچیدگی و کاربرد بایکدیگر متفاوت هستند. در فرآیند تزریق پلاستیک از انواع ترکیبات پلاستیکی مانند پلیکربنات، پلیاستایرن، پلیاتیلن، پلیپروپیلن، پلی وینیلکلراید، اکریلیک و تفلون برای تولید محصول نهایی استفاده میشود.
فرآیند قالبگیری تزریقی نیاز به استفاده از دستگاه قالبگیری تزریقی، مواد پلاستیکی خام و قالب دارد که شرح مراحل فرآیند قالب گیری تزریقی به صورت کامل و جامع در مقالهای جداگانه آورده شده که میتوانید از اینجا آن را مطالعه کنید.
سازوکار دستگاه قالب سازی پلاستیک:
لبههای دستگاه قالبگیری تزریقی را میتوان به صورت افقی یا عمودی بست.
اکثر دستگاهها به صورت افقی بسته میشوند، اما دستگاه تزریق عمودی در برخی از کاربردها مانند قالب ریزی و ساخت یکسری سازهها استفاده میشود، که به دستگاه اجازه میدهد از جاذبه زمین استفاده کند. بعضی از دستگاههای عمودی نیز نیازی به بستن قالب ندارند.
روشهای زیادی برای بستن روی صفحه وجود دارد که معمولترین آنها گیرههای دستی است (هر دو نیمه به صفحهها پیچ میشوند).
با این حال گیرههای هیدرولیکی (از چوک ها برای نگه داشتن ابزار در جای خود استفاده میشود) و گیره های مغناطیسی نیز استفاده میشود. گیرههای مغناطیسی و هیدرولیکی در مواردی که نیاز به تغییر سریع ابزار باشد مورد استفاده قرار می گیرند.
دستگاه قالب سازی پلاستیک به ۲ بخش تقسیم بندی میشود:
بخش اول گیره دستگاه و بخش دوم قسمت تزریق.
عملکرد واحد گیره، باز و بسته کردن قالب و بیرون انداختن محصولات است.
۲ نوع روش باز و بست وجود دارد، مکانیزم این دستگاه بدین صورت است که ابتدا در بخش گیره (بخش دورچین شکل زیر)، گیره به صورت دستی و در ادامه قسمت تزریق قالب مستقیماً با یک سیلندر هیدرولیکی باز و بسته میشود.
اجزای اصلی دستگاه قالب سازی پلاستیک:
دستگاه های تزریق پلاستیک از قیف تغذیه، مته مارپیچی و واحد حرارتی تشکیل شدهاند. در واقع قالبها در صفحات گیرهی دستگاه قفل شده و سپس پلاستیک از دهانه اسپرو به داخل قالب تزریق شده و در نهایت قطعه تزریقی ایجاد میشود . به صورت دقیقتر اجزا این دستگاه به شرح ذیل است:
- واحد تزریق:
از چند جزء اصلی تشکیل شده است:
- موتور اسکرو یا موتور با پیچ بیرونی.
- پیچ و بشکه رفت و برگشتی.
- بخاری ، ترموکوپل ، پیستون حلقه ای.
- ورق صفحه ای (پیچ RR).
- واحد گیره.
- قالب.
- گیره بیرونی موتور.
- میله های راهنما.
کاربرد دستگاه قالب سازی پلاستیک:
در قالب تزریق پلاستیک از رزینهای پلاستیکی گرانول یا گلولهای شکل برای تولید محصولات مختلف از اجزای خودرو و هواپیما گرفته تا ظروف نگهداری، قطعات آلات موسیقی و شانههای مو استفاده میشود. از دستگاه تزریق پلاستیک برای تولید قطعات پلاستیکی دیواره نازک برای کاربردهای بسیار متنوع استفاده میشود که یکی از رایج ترین آنها پلاستیک است.
محفظه پلاستیکی یک محفظه دیواره نازک است در محصولات مختلفی از جمله لوازم خانگی، وسایل الکترونیکی مصرفی، ابزار برقی و همچنین در ساخت داشبورد خودرو مورد استفاده قرار میگیرند. سایر محصولات رایج دیواره نازک شامل انواع مختلف ظروف باز ، مانند سطلها است.
از دستگاه تزریق برای تولید چندین مورد روزمره مانند مسواک یا اسباب بازی های کوچک پلاستیکی نیز استفاده می شود. علاوه بر این بسیاری از دستگاههای پزشکی، از جمله دریچهها و سرنگها، با استفاده از این دستگاه تولید میشوند.
عمده کاربرد این دستگاهها در ایران به تولید انواع سبد میوه، گلدان، سطل، ظروف آشپزخانه پلاستیکی، قطعات خودرو و … اختصاص دارد. از این رو معمولاً نام این دستگاه در کنار محصول نیز بکار می رود. بعنوان مثال دستگاه تزریق پلاستیک سبد میوه و….
انواع دستگاه قالب سازی پلاستیک:
دستگاه تزریق عمدتاً براساس میزان قدرت گیره طبقه بندی میشوند. درحقیقت هر اندازه قدرت گیره دستگاه بالاتر باشد، امکان تولید قطعات بزرگتر و سنگینتر را فراهم میآورد. پارامتر های مهم دستگاه عبارتند از:
- قدرت گیره.
- ظرفیت واحد تزریق.
- فاصله بین میله های راهنما.
- کورس بازشو گیره.
- حداقل و حداکثر ارتفاع قالب.
دستگاههای قالبگیری به ۳ دسته کلی هیدرولیکی ، برقی و هیبریدی تقسیم بندی میشوند، که در ادامه به صورت اختصار با این ۳ دستگاه بیشتر آشنا خواهیم شد.
۱- دستگاه تزریق پلاستیک هیدرولیکی:
دستگاه قالبگیری هیدرولیک از نظر تاریخی تنها گزینه در دسترس سازندگان بوده است تا اینکه یک شرکت تولید کننده این وسایل در ژاپن اولین ماشین الکتریکی را در اوایل دهه ۱۹۸۰ معرفی کرد. در اینجا برخی از مزایای دستگاه قالبگیری تزریقی تمام هیدرولیک آورده شده است:
- قیمت پایین.
- قیمت پایه این دستگاهها به طور قابل توجهی کمتر از گزینههای دیگر آن است.
- قطعات ارزان تر.
- اگر به دلیل خرابی قطعهای روی دستگاه تعویض شود یا طول عمر قطعات به اتمام برسد، قطعات تعویض هم آسانتر هم با هزینه کمتری پیدا میشوند.
- قطعات قویتر.
- قطعات هیدرولیکی دستگاه در برابر سایش مقاوم ترند، لذا دوام بیشتری از سایر همنوعان خود دارد.
- قدرت.
- دستگاه قالبگیری هیدرولیک دارای نیروی بستن استثنایی هستند.
۲- دستگاه تزریق پلاستیک الکتریکی:
همانطور که در بالا گفته شد، دستگاههای تزریق پلاستیک الکتریکی برای اولین بار در دهه ۱۹۸۰ ساخته شدند و به سرعت محبوبیت خود را پیدا کردند. در ادامه برخی از مزایای دستگاه قالبگیری تزریقی تمام الکتریکی بیان شده است:
- بهره وری انرژی.
- این دستگاهها هنگامی کار میکنند که از انرژی برق استفاده کنند، یعنی خروجی موتور فقط برابر با بار مورد نیاز است.
- زمان کمتر.
- در این مدل هیچ گونه نشتی روغنی وجود ندارد. همچنین، عدم استفاده از روغن به معنای عدم تعویض فیلتر است که خود باعث کاهش هزینههای مصرفی میشود.
- فرآیند سریعتر.
- این دستگاهها به صورت دیجیتالی کنترل میشوند به این معنی است که فرآیند کاملاً قابل تکرار است و نیازی به نظارت ندارد.
- عملکرد تمیز.
- از آنجا که برای این دستگاه از روغن استفاده نشده است، در صورت ساخت قطعات پزشکی استفاده از این دستگاه امری بیخطر است. معمولاً، این قطعات باید در بخش جدا و تمیز اتاق ساخته شوند.
۳_ دستگاه قالب سازی پلاستیک هیبریدی تلفیقی از دو دستگاه برقی و هیدرولیکی است و تمامی مزایای آن دو دستگاه را به صورت یکجا دارد اما با هزینه بالاتر.
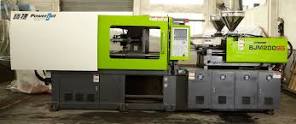
خط تولید ظروف یکبار مصرف پلاستیکی:
امروزه انواع ظروف یکبار مصرف نفوذ بسیاری در زندگی روزمره انسان ها پیدا کرده است. بنابراین شناخت خط تولید و شناخت
مراحل ساخت ظروف یکبار مصرف و راه اندازی کارخانه ظروف یکبار مصرف مفید به نظر می رسد. در این مقاله برآنیم تا شما را با
مراحل تولید انواع ظروف یکبار مصرف که یکی از پر کاربردترین ابزار مورد استفاده در زندگی بشری است، آشنا سازیم. ظروف یکبار
مصرف از کاغذ، پالستیک و مقوا ساخته شده و به صورت بطری، لیوان، بشقاب و …. از پلیمر های گوناگون ساخته شده است.
مواد پلیمری در بسیاری از امور که به طور مستقیم یا غیر مستقیم با سالمت انسان ها سر و کار دارد، مورد استفاده قرار گرفته
اند؛ به طوری که گاهی حیات انسان ها در بسیاری از علوم مخصوصا علم پزشکی وابسته به همین مواد پلیمری است. در بین
کاربردهای فراوان و مختلف مواد پلیمری، ظروف یکبار مصرف نقش ویژه ای در زندگی ما انسان ها را به خود اختصاص داده
است.
انواع قالب های ترموفرمینگ ظروف یکبار مصرف
قالبهای پرس ترموفرمینگ از نوع فرمینگ بوده و نسبت به سایز پرس و ابعاد فرم دهی پرس دارای کبیته های مختلف برای یک
ظرف یکسان هستند .
معموال ظروف بصورت کلی دارای ابعاد دهنه استانداردی میباشند .
تحلیل صنعت تولید ظروف یکبارمصرف پلاستیکی:
موانع و مشکالت تولید ظروف یکبار مصرف پالستیکی.
مشکالت تهیه مواد ولیه.
نوسانات قیمت مواد اولیه.
مزیت ها و نقاط قوت تولید ظروف یکبار مصرف پالستیکی.
بازار مصرفی رو به رشد.
شلک پذیری باال.
(دستگاه پرس ترمو فرمینگ )برای تولید ظروف یکبار مصرف از ورق آماده پرس ترموفرمینگ ، بعنوان مرحله و دستگاه دوم از خط تولید ظروف یکبار مصرف با استفاده از سیستم ترموفرمینگ میباشد.
در این دستگاه ورق تولید شده بصورت رول آماده وارد دستگاه شده و پس از عبور از کوره برقی والزمه جهت فرم دهی ، در قسمت پرس اصلی و در زیر قالب ، با استفاده از فشار باد ورق گرم ، حالت و فرم قالب را به خود گرفته وظرف تولیدی ، بالفصله خنک و پس از برش از ورق اصلی جدا و بصورت محصول نهایی از قالب خارج میگردد .
در ادامه نیز
بصورت دستی و یا بصورت اتوماتیک در دستگاه استکر )لیوان جمع کن ( دسته بندی میگردد . مابقی ورق نیز بصورت ضایئات و
بشلک رول در آمده ، تا پس از آسیاب و خرد شدن ، دوباره در دستگاه تولید ورق با مخلوط شدن با مواد اولیه نو تبدیل به ورق
جدید شود
نحوه ساخت ظروف یکبار مصرف:
استفاده درست از ظروف یکبار مصرف پلیمری و اهمیت تفکیک زباله از مبدأ توسط مردم و فرهنگ سازی کردن آن بر اساس
دستورالعمل های موجود و همچنین توجه ویژه به بازیافت صحیح ظروف یکبار مصرف پلیمری توسط کارشناسان و مسئولین
مربوطه امری ضروری است.
تشریح تولید ظروف یکبار مصرف:
فرآیند تولید ظروف یکبار مصرف در همه جا به یک شلک بوده و تنها در استفاده از ماشین آالت و روش های فرعی بکار برده شده
متفاوت است. فرآیند اصلی تولید در دو مرحله خالصه می شود. ابتدا مواد اولیه مورد نظر اعم از: گرانول و پودر و…. در دستگاه
اکسترودر تبدیل به ورق شده و سپس ورق مورد نظر به شلک دلخواه تبدیل می شود.
به طور کلی در کارخانه تولید ظروف یکبار مصرف ، تولید ظروف یکبار مصرف از دو طریق صورت می گیرد:
تولید ظروف یکبار مصرف با سیستم تولید نیمه فرمینگ.
تولید ظروف یکبار مصرف با سیستم تولید ترموفرمینگ.
تولید ظروف یکبار مصرف با سیستم تولید نیمه فرمینگ.
در این نوع خط تولید، تمامی فرآیند تولید و آماده سازی در یک دستگاه انجام می گیرد. مواد اولیه که به شلک گرانول پتروشیمی
در بخشی از خط تولید به نام اکسترودر، ذوب شده و تبدیل به ورق گرم می شود. قبل از سرد شدن این ورق، البته با توجه به
امکانات و نوع این دستگاه، بدون یکنواخت شدن مواد، ورق گرم وارد بخش پرس شده و در زیر قالب عملیات فرم دهی ورق و
تولید نوع مورد نظر ظروف یکبار مصرف قرار می گیرد.
تولید ظروف یکبار مصرف با سیستم تولید ترمو فرمینگ:
در این نوع تولید، محصول با کیفیت باالتری نسبت به تولید با سیستم نیمه ترموفرمینگ حاصل می شود. در تولید با سیستم
ترمو فرمینگ برخالف تولید با نیمه ترموفرمینگ دو دستگاه در حال انجام فرایند می باشند. به این صورت که در دستگاه اول مواد
اولیه)گرانول و پودر و…( به ورق تبدیل شده و به صورت رول تولید می شوند و در دستگاه دومی که پرس ترمو فرمینگ نام دارد،
ورق تولید شده را با عبور دادن در کوره و رساندن به درجه حرارت استاندارد جهت فرم گیری وارد بخش پرس شده و در زیر قالب
تولید ظروف قرار می گیرد.
این روش یکی از فرآیندهای پیشرفته برای شلک دهی به محصوالت پالستیکی می باشد که از فشارهای مثبت هوا جهت وارد کردن
نیرو بر ورق گرم برای قالب گیری استفاده می شود.
مراحل ترمو فرمینگ به تفکیک:
ورقه پالستیک گرم می شود.
ورق های گرم شلک خاصی به خود گرفته است.
اشکال برش داده می شوند.
واردات، صادرات و مواد اولیه:
صادرات بسیاری به کشورهای آسیای میانه و افغانستان از این منطقه صورت میگیرد. صادراتی که به کشورهایی چون اروپا هم
صورت میگرفته اما با تحریمها کمرنگ شده، ولی دوباره درهای صادراتی این کاالی ایرانی باز شده است.
در حال حاضر به صورت پیوسته و دائم نمیتوانیم این حجم باال را تأمین کنیم و مشکالتی نیز در مورد بستهبندی کاالی صادراتی
در این زمینه داریم که البته درصدد رفعشان هستیم.
اما باید تأکید کنم که این حوزه ظرفیتهای باالیی برای ارزآوری دارد و با توجه به اینکه مواد اولیه آنکه عمدتا مواد پتروشیمی است هم بیش از ۹۰درصد در کشورمان تولید میشود و ارزشافزوده باال و ارزآوری قابل توجهی نصیب کشورمان میکند. بنابراین کسانی که نگاهی انتقادی به این حوزه دارند باید همه جنبههای این کار رامدنظر داشته باشند.
وی همچنین در پاسخ سوالی مربوط به حجم واردات در این حوزه میگوید: واردات قابل ذکری در این حوزه نداریم مگر اینکه کاالیی بسیار فانتزی باشد و تولیدش در ایران وجود نداشته باشد که در مقابل حجم تولید داخلی به چشم نمی ایند.
آشنایی با خط تولید دستگاه قالب سازی و ظروف و قطعات پالستیکی به روش IML:
تمامی فعاالن عرصه تولید متفق القول معتقدند که مشتریان فروشگاه ها که همان مصرف کنندگان نهایی باشند به خوبی از نیاز
خود آگاهند و می دانند چرا به سوپر مارکت آمده اند پس تنها کاری که برای تولید کننده باقی می ماند، البته پس از تولید
نیازمندی های مصرف کنندگان، جلب توجه آنان به بهترین شلک ممکن است.
وقتی یک مشتری با چشمان جستجوگر خود درروی قفسه های فروشگاه به دنبال خمیردندان می گردد، پیداست که نیاز خود را مشخص کرده و فقط در جستجوی چشمگیرترین یا جذاب ترین بسته بندی است و شاید در این راه حتی توجه چندانی نیز به نوع عملکرد محصول یا کیفیت آن نداشته باشد.
باتوضیحات مذکور پرواضح است که چرا صاحبان برند چرا این مقدار وقت و هزینه را صرف پیدا کردن راه هایی بهتر برای انجام
عملیات لیبل زنی و کیفیت باالتر طرح های گرافیکی روی لیبل ها می نمایند. پس از سال ها تحقیق و ابداع روش های گوناگون
یک روش خیلی بیشتر از دیگران به چشم آمد و توجه همگان را به خود جلب نمود.
در این روش لیبل درون قالب قرار می گرفت و همزمان با تولید ظرف، طرح گرافیکی و لیبل نیز بر روی آن پیاده می شد و بعدها به IML شهرت یافت. ابداع روش IML به اوایل دهه ۱۹۸۰ باز می گردد که پس از شناسانده شدن به صنعت بسته بندی، به سرعت محبوبیت باالیی برای خود کسب نمود.
هم اکنون ۸۵ تا ۹۵ %از تمامی محصوالت غذایی با روش IML بسته بندی می شوند که با توجه به جوانی این متد، نشان از رشد
بسیار باالی آن دارد. اما در آمریکای شمالی، IML کار خود را در صنعت مواد شوینده آغاز نمود و برای اولین بار بر روی بطری های
پالستیکی تزریقی از آنها استفاده شد.
پس از آن و با انجام اطالع رسانی بهتری که در مورد آن انجام شد، در صنایع دیگر از جمله صنایع غذایی نیز مورد استفاده گسترده قرار گرفت.
بد نیست اشاره کوتاهی به نوع انجام کار داشته باشیم. لیبل های چاپ خورده و آماده درون قالب ها تزریق قرار گرفته و به وسیله پمپ های وکیوم، در محل دلخواه نگه داشته می شود تا رزین پالستیک درون قالب تزریق شده ولیبل را احاطه کند.
سپس قالب کار خود را انجام داده و محصول نهایی تولید می شود. تمایز اصلی این روش با روش های دیگر در این است که در IML لیبل بخشی از بدنه بسته بندی است در حالی که در روش های دیگر، نیاز به چسب برای چسبانیدن لیبل بر روی ظرف می باشد.
شاید این توضیح کوتاه، IML را روشی بسیار ساده جلوه دهد که تمامی تولید کنندگان به راحتی قادرند از آن در فرآیند تولید خود
سود ببرند ولی این گونه نیست و این روش نیز پیچیدگی های خاص خود را دارد.
خرید خطوط تولید IML کاری است بسیار آسان ولی فرآیند یادگیری کاربری دستگاه های آن تا حد بسیار زیادی پیچیده است. در حقیقت اگر این فرآیند به صورت صحیح طی نشود، ماشین آالت خریداری شده از بازدهی الزم برخوردار نخواهد بود به دلیل حساسیت بسیار باالی ماشین آالت و تجهیزات IML ،شرکت خریداری کننده، می بایستی از پرسنل بسیار زبردست وماهری برای کار با دستگاه ها برخوردار باشد.
به زبان ساده تر خریداری دستگاه ها فاز اول کار و استخدام و استفاده از نیروی کاری که مهارت الزم را دارا باشد، فاز دوم. یکی دیگر از مشکالت کار با تجهیزات IML ،میزان ضایعات در حین تولید است. بسیاری ازشرکت هایی که شروع به استفاده از این روش می نمایند، در سال اول کار خود، ممکن است تا ۲۰ %ضایعات داشته باشند که این امر کامال اجتناب ناپذیر است.
اولین شرکتی که در آمریکای شمالی اقدام به استفاده از IML نمود، شرکت کانادایی IPL بود.این شرکت در سال ۱۹۳۹در شهر Damein St در ایالت کبک کانادا تاسیس شد. بعدها شهر Damein St به دره پالستیک شهرت یافت چرا که یکی از بزرگ ترین تولید کنندگان محصوالت پالستیکی یعنی IPL در آن واقع بود. اولین تجربه IPL در استفاده ازفناوری IML به اوایل دهه ۱۹۹۰ باز می گردد.
آنها از این روش در تولید ظروف دو الیه روغن مارگارین استفاده نمودند که در آن زمان جدیدترین ظرف به شمار می آمد. درحقیقت مدیران شرکت همواره سعی داشته اند تا نوآوری بخشی از هویت شرکت باشد. البته آنها نیز مانند تمامی شرکت های دیگر در ابتدای کار خود با IML بامشکالتی مواجه بودند
و طرح جدیدشان از موفقیتی که انتظارش را داشتند برخوردار نبود ولی هم اکنون ظرف ابداعی آنان، همان چیزی است که در تمامی صنایع مایعات خوراکی مورد استفاده است و به اصطالح به ظروف دردار شهرت دارند.
هم اکنون آنان خود را به عنوان موفق ترین و بزرگ ترین تولید کننده ظروف IML در قاره آمریکا مطرح نموده اند.این روش از هر لحاظ برتری های محسوس نسبت به روش های متداول دارد که از آن جمله می توان به تنوع بسیار باالی رنگ وطرحی که IML ارایه می دهد اشاره نمود.
در کنار کیفیت بسیار باالی رنگ و عکس چاپ شده بر روی ظرف، هزینه های تولید نیزبه صورت چشم گیری کاهش پیدا می کند چرا که دیگر نیازی به تولید برچسب و لیبل و استفاده از چسب یا فشار برای چسباندن طرح بر روی ظرف نیست.
تمامی شرکت هایی که در حال استفاده از IML به صورت موفقیت آمیز هستند به ۳ فاکتور آن بیش ازدیگر مزایایش اشاره دارند. این ۳ فاکتور عبارتند از: مقاومت بسیار باالتر در برابر آب و سطوح خشن، زیبایی بسیار چشم گیر و قیمت بسیار رقابتی و به صرفه IML یکی از ویژگی های IML که به هیچ وجه قابل قیاس با دیگر انواع روش های لیبل زنی است،ظاهر منحصربه فردی است که ازمحصول ارایه می دهد چرا که خریدار تصور می کند.
هیچ لیبلی بر روی ظرف وجود ندارد. به قیمت بسیار به صرفه IML اشاره کردیم، بد نیست بدانید وقتی صحبت از انجام لیبل زنی در حین تولید ظرف می کنیم، دیگر نیازی به خرید دستگاه های لیبل زن و یا حرارتی برای چسباندن لیبل نیست و با استفاده از یک دستگاه، تمامی کارها انجام می پذیرند.
یکی دیگر از عوامل کیفیت باالی عکس های چاپ شده در روش IML ،چاپ لیبل ها به صورت افست ۱۷۵ خطی است، این در حالی است که برای چاپ لیبلهای عادی، از دستگاه های افست ۸۰ خطی استفاده می شود.
به دلیل کیفیت باالتر رنگ، طرح لیبل نیز به صورت دقیق تری چاپ شده و توهم واقعی بودن را هر چه بیشتر به چشمان بیننده انتقال می دهد. گفتنی است که برای چاپ برچسب های عادی از دستگاه های چاپ flexo یا offset Direct استفاده می شود. در نهایت تنظیم میزان شفافیت یا مات بودن طرح و عکس نیز کاری است بسیار آسان.
می توان ادعا کرد که IML خود کمکی است در جهت حفظ محیط زیست چرا که وقتی ظاهر بسته بندی زیباست و این زیبایی به
راحتی از بین نمی رود، مصرف کننده نهایی قادر است از ظرف برای مقاصد دیگر نیز بهره ببرد و به این ترتیب استفاده از انرژی
صرف شده به صورت بسیار بهینه تری انجام می پذیرد و زباله کمتری نیز تولید می شود.
با توجه به دوام بسیار باالی عکس روی ظرف و قابلیت استفاده دوباره از ظرف بسته بندی، عملیات بازاریابی نیز به صورتی خودکار و برای مدت زمان طوالنی انجام می پذیرد. این یعنی تبلیغات کامال رایگان که خود ره آوردی است از فناوری IML .یکی از فناوری هایی که برای مدت بسیار کوتاهی خود را به عنوان رقیب IML مطرح نمود.
فناوری انتقال لیبل به صورت گرمایی )transfer heat )بود ولی خیلی زود بازار را برای رقیب قدرت مند خود خالی گذاشت چرا که IML لیبل را به صورت کامل بر روی ظرف پیاده می کند و تمامی سطح ظرف را می پوشاند در حالی که transfer heat بخش هایی از باال و پایین ظرف را خالی می گذارد و البته از انرژی کمتری نیز در انجام عملیات لیبلینگ استفاده می کند.
به عالوه این که در روش IML فقط با استفاده از یک لیبل، می توان تمامی ۴ طرف بسته بندی و حتی روی درب و کف ظرف را نیز به صورت یکپارچه چاپ نمود ولی transfer heat قادر به انجام چنین کاری نیست. از دیگر ضعف های می توان به دوام کم در برابر خراشیدگی ها، اشیاء تیز و جمع شدن و چروک خوردن اشاره نمود.
لیبل های IML در برابر گرما از مقاومت باالیی برخوردارند و حتی ظروف دارای این نوع لیبل را می توان در مایکروویو نیز استفاده
کرد.
هم اکنون بازار مصرف IML در آمریکای شمالی به شدت رو به افزایش است و صاحبان برندهای مختلف در حوزه های مختلف
تولید در حال یافتن راه هایی جدید برای استفاده از آن برای عرضه هر چه بهتر محصوالت خود می باشند.
حتی شرکت های تولیدی رنگ و رزین، محصوالت شیمیایی مورد استفاده در استخرها، انواع نوشیدنی های میوه ای و در نهایت انواع محصولات لبنی نیز روی به استفاده از این روش جذاب و مقرون به صرفه آورده اند. همان طور که از نمونه های مذکور بر می آید هیچ
محدودیتی برای استفاده از IML در صنایع بسته بندی وجود ندارد .
تقریبا هر محصولی را می توان با استفاده از IML بسته بندی و روانه بازار نمود. برخی کارشناسان IML را همه چیز می دانند، چرا که فقط با تغییر نوع بسته بندی به IML ،یک شرکت می تواند به چند هدف مهم است پیدا کند که از آن جمله به تمایز در ظاهر، انجام بازاریابی به صورت خودکار و بدون صرف حداقل هزینه اضافی و در نهایت زیبایی منحصر به فرد به همراه رنگ های بسیار طبیعی و متنوع اشاره نمود.
شرح فرآیند تولید و تکنولوژیهای موجود:
برآیند برچسب گذاری درون قالبی به روش تزریق بهره گیری از برچسب گذاری درون قالبی در فن آوری قالب گیری تزریقی مزایای فراوانی برای تولید کننده، عرضه کننده و مصرف کننده نهایی به همراه دارد. با استفاده از این روش مرحله ثانویه برچسب گذاری در فرآیند تولید حذف می شود، عالوه بر اینکه برچسب درون قالبی جزئی دائمی از ظرف شده و امکان کنده شدن آن وجود ندارد.
در فرآیند برچسب گذاری درون قالبی به روش تزریق، فیلم برچسب که سطحی صاف دارد در ضمن فرآیند تزریق پالستیک مذاب،جزئی از بدنه ظرف می شود. در مواردی که به خاطر طراحی ویژه ظرف، برچسبی با انعطاف پذیری باال مورد نیاز است اغلب از برچسب های درون قالبی استفاده می شود.
این برچسب های معموال فیلمی از جنس پلی پروپیلن با ضخامت ۵۰ تا ۱۰۰میکرومتر است که محتوای برچسب روی فیلم چاپ شده است.
شلک زیرنشان دهنده مراحل برچسب گذاری درون قالبی به روش تزریق است. در این فرآیند ابتدا برچسب در قالب باز جاسازی
شده و توسط نازل های خالء، خاصیت جذب الکترواستاتیکی یا وسایل دیگر در محل مورد نظر ثابت نگهداشته می شود.
سپس
قالب بسته شده و رزین پالستیکی گداخته شده، درون قالب تزریق می شود تا شلک ظرف مورد نظر را پیدا کند. به محض اینکه
دمای رزین پالستیکی به سطح مناسب برای خروج از قالب برسد، آماده خروج از قالب می شود. این کار معموال با استفاده از
روبوت انجام می شود.
با این که تکنیک های زیادی در رابطه با فن آوری IML ظهور کرده است، یکی از مهم ترین مالحظات مرتبط با این فن آوری
چگونگی ثابت نگه داشتن برچسب در قالب به هنگام تزریق مواد است. در بسیاری از موارد، استفاده از ابزارهای تولید شارژ
الکترواستاتیکی نسبت به استفاده از نازل های خالء برای نگه داشتن برچسب در محل مورد نظر در محفظه قالب، به صرفه تر و
قابل اعتمادتر است.
بهره گیری از روش مذکور مزایای مشخصی برای کمپانی قالب گیری، مشتریان آنها و مصرف کننده نهایی
دارد. در ادامه کلیات استفاده از دو روش مذکور مورد بحث قرار می گیرد
ثابت نگه داشتن برچسب به کمک نازل های خلاء:
اولین موضوع، چگونگی دخیل کردن کانال ها و نازل های خالء در سیستم قالب گیری است. طراحی و تولید قالب هایی ویژه برای
این کار هزینه تجهیزات مورد استفاده را به شلک قابل توجهی افزایش می دهد.
به علاوه، برچسب هم باید قوام و استحکام کافی
داشته باشد تا داخل نازل خالء، نشود؛
این اتفاق می تواند شلک سطح ظرف را تغییر دهد یا باعث برآمده شدن بخشی از آن که
برچسب را در به داخل خود کشیده است شود. توجه به این نکته نیز بسیار حایز اهمیت است که سیستم روبوتیک، برچسب را
گم نکند و برچسب حتما در محل مشخص شده قرار داده شود.
در صورتی که برچسب در محل مشخص شده قالب قرار نگرفته
باشد و مواد پالستیکی داخل قالب تزریق شود مشکالت زیادی را ایجاد خواهد کرد و باید زمان و هزینه زیادی برای خارج کردن
ظرف قالب گیری شده
از درون محفظه قالب و تمیز کردن کانال ها و نازل های خالء صرف شود. اگر برچسب طی فرآیند قالب
گیری شکسته شود یا اینکه از محل خود جابه جا شود، ممکن است پالستیک مذاب به داخل نازل های خالء کشیده شده و باعث
ایجاد وقفه در فرآیند قالب گیری شود. به منظور جلوگیری از این موضوع باید ابزاری برای مشخص کردن وضعیت سیستم خالء و
توقف تزریق پلیمر در صورت بروز اشکال در نظر گرفته شود. مشلک دیگر این روش نگه داشتن برچسب این است که کانال های
خالء در قالب های دوگانه ممکن است موجب برهم خوردن یکنواختی دمای پالستیک قالب گیری شده شود. برچسب را میتوان به
کمک کانال های خالء تولید شده با فلز تخت شده )metal sintered )در محل مناسب خود ثابت نگه داشت
مراحل انجام کار به این قرار است: یک روبوت برچسب را از مخزن برچسب ها)magazine label )جدا می کند و آن را در محل
مورد نظر در محفظه قالب قرار می دهد، سپس سیستم خالء روشن شده و شروع به کار می کند و درنهایت پالستیک مذاب به
درون محفظه قالب تزریق می شود. استفاده از روش خالء هنگامی بیشترین سودمندی را دارد که شلک قالب، استفاده از
برچسب هایی را که از پیش شلک داده شده اند، طلب کند یا اینکه نیاز به استفاده از برچسب های ضخیم باشد. به همین ترتیب هنگامی
که نیاز به استفاده از برچسب یا قالبی باشد که سطح ناصاف و طرح دار دارد، استفاده از سیستم خالء گزینه مناسبی است.
استفاده از برچسب های نسبتا نازکی که حاوی افزودنی های ضد الکتریسیته ساکن باشد فرآیند استفاده از سیستم خالء در IML را
ساده تر می کند و از به هم چسبیدن برچسب ها در اثر الکتریسیته ساکن جلوگیری می کند.
ثابت نگه داشتن برچسب به کمک الکتریسیته ساکن
استفاده از الکتریسیته ساکن برای ثابت نگه داشتن برچسب طی فرآیند قالب گیری تزریقی، نیاز به استفاده از نازل های خالء که
هزینه بیشتری را برای تولید و نگهداری قالب ایجاد می کند، رفع می کند. در برچسب گذاری درون قالبی با قالب مجهز به کانال
های خالء، وجود الکتریسیته ساکن در برچسب ها یک عامل ناخواسته است.
در تکنیک چسباندن برچسب به قالب با استفاده از خاصیت جذب الکترواستاتیکی، کنترل بار الکترواستاتیکی برای کار با برچسب و ثابت نگه داشتن آن طی فرآیند تزریق پالستیک امری ضروری است.
الکتریسیته ساکن به معنای عدم تعادل بار الکتریکی در یک ماده است به این معنی که اندازه یکی از بارهای الکتریکی منفی یا مثبت در آن از دیگری بیشتر شود. سطحی که بار الکتریکی منفی دارد الکترون های بیشتری نسبت به حالت عادی دارد و به همین ترتیب تعداد الکترون های سطحی که بار مثبت دارد، کمتر از سطح بدون بار است. سطح باردار میدان الکترواستاتیکی ایجاد می کند.
خطوط میدان از تمام نقاط سطح به شلک عمودی خارج می شود. الکتریسیته ساکن در طول خود سطح باردار یا جریانی ندارد یا این که بسیار آهسته جابه جا می شود، این موضوع به معنای افزایش بار الکتریکی یا انباشته شدن آن در برخی از نقاط سطح ضمن کار با آن است. شدت میدان الکتریکی بر حسب نیرویی که یک ذره باردار فرضی در صورت قرار گرفتن در میدان تحمل می کند، تعریف می شود.
شدت میدان الکتریکی که با حرف E نشان داده می شود، در هر نقطه از یک سیستم الکترواستاتیکی برابر است با نیرویی که بر ذره دارای یک واحد بار الکتریکی مثبت در آن نقطه وارد می شود. به این ترتیب چنانچه بار نقطه ای q در نقطه ای از میدانی قرار گیرد که شدت میدان در آن نقطه برابر E باشد، نیرویی برابر qE=F به بار نقطه ای
وارد می شود.
یکای شدت میدان برابر است با: ۱ m/V ۱= As/Nm ۱=C/Newton .در عمل معموال به جای ولت بر متر از کیلوولت بر متر m/kV
استفاده می شود. در هر نقطه از یک میدان جهت خطوط میدان بر حسب جهت بردار مماس بر خط میدان در آن نقطه تعریف می شود و تراکم خطوط میدان در یک محل نشان دهنده شدت میدان در آنجا است.
در فرآیند الکترواستاتیکی )IML با استفاده از نگهدارنده های الکترواستاتیکی( ابتدا روبوتی با استفاده از مکش )suction )برچسب
را از صفحه برچسب ها جدا می کند. بار الکتریکی زیادی در برچسب ذخیره می شود و برچسب به کمک بازوی روبوتیک
)tool arm-of-End=EOAT )به سطح محفظه قالب نزدیک می شود. سپس بازوی روبوتیک برچسب را در محل در نظر گرفته شده
قرار می دهد،
ساکشن خالء برچسب را رها می کند و برچسب در محل مورد نظر، به سطح محفظه قالب میچسبد. در این مرحله
دیگر نیازی به سیستم خالء محفظه قالب یا وجود ماده چسبنده بر سطح برچسب نیست .
وقتی برچسبی که از مواد و طراحی مناسب برخوردار است باردار شود، به واسطه خاصیت جذب الکترواستاتیکی به سطح فلزی قالب که نقش زمین را بازی می کند می چسبد.
برچسب می تواند تا چند دقیقه با میزان چسبندگی عالی به سطح محفظه قالب
بچسبد. یکی از موارد احتیاط به هنگام شارژ برچسب، عدم استفاده از جوهر یا پوشش ضداستاتیکی در ساخت برچسب است.
برچسب های مورد استفاده در این روش عموما باید خاصیت باالی دی الکتریک داشته و کامال نارسانا باشند.
برای استفاده از جذب با خاصیت الکترواستاتیکی و بهره گیری از همه مزایای این روش وجود اجزای زیر ضروری اسـت:
• روبوتی با بازو و سیستم انتهای بازوی روبوتیک )EOAT)
• مخزن برچسب )magazine label)
• منبع تغذیه ولتاژ باالی DC با ظرفیت خروجی قابل تنظیم برای بارگذاری
• اعمال کننده ای شارژر
• برچسب های ساخته شده با مواد وطراحی مناسب جهت پذیرش و نگهداری بار الکتریکی
روش متداول، اعمال کننده شارژر در انتهای بازوی روبوتیک
این روش قابل اطمینان بوده و کارایی باالیی دارد اما برای طراحان و تولید کنندگان بازوی روبوتیک قدری چالش انگیز است.
در این روش اعمال کننده شارژر، در داخل ادوات انتهای بازوی روبوتیک طراحی می شود و در واقع بخشی از این تجهیزات است. این اعمال کننده می تواند یک میله مستقیم بارگذاری با تعدادی پین برای انتشار میدان الکترواستاتیکی باشد یا اینکه ممکن است از یک سری ساطع کننده مجزا تشکیل شود.
تعداد و نوع اعمال کننده هایی که مورد نیاز است، بستگی به اندازه و شلک برچسب و همین طور شلک هندسی محل جاسازی برچسب در محفظه قالب دارد. وقتی که برچسب به وسیله دریچه های مکنده نصب شده در انتهای بازوی روبوتیک نگه داشته می شود، اعمال کننده های شارژر درست پشت برچسب واقع می شود.
میله های ساطع کننده میدان الکترواستاتیکی در فاصله ۱ اینچی و رو به پشت برچسب قرار میگیرند. وقتی که روبوت برچسب را در محل مورد نظر از سطح قالب قرار می دهد، منبع تغذیه اعمال کننده به مدت تقریبی ۲ الی ۴ ثانیه روشن می شود.
به این ترتیب برچسب بار الکترواستاتیکی پیدا می کند و به واسطه خاصیت جذب الکترواستاتیکی بالفاصله به سطح فلزی قالب که نقش زمین الکتریکی را ایفا می کند می چسبد. دستگاه خالء خاموش می شود و روبوت ابزار بازوی روبوتیک را برای انجام چرخه بعدی از قالب بیرون می آورد.
در طراحی بازوی روبوتیکی که اعمال کننده شارژر را درون خود جای می دهد باید چند نکته را مد نظر قرار داد. چون بخش ساطع کننده اعمال کننده باید ۱ اینچ از برچسب فاصل داشته باشد، حتما الزم است هر جزء فلزی بازوی روبوتیک به زمین )الکتریکی(متصل شود و الاقل ۱/۵ اینچ از بخش ساطع کننده فاصله داشته باشد.
هر جزء فلزی که فاصله ای کمتر از ۱/۵ اینچ تا ساطع کننده داشته باشد بخشی از میدان الکترواستاتیکی تولید شده توسط اعمال کننده را به خود جذب می کند و موجب می شود برچسب الکتریسیته ساکن کمتری پیدا کند.
اگر در طراحی بازوی روبوتیک تعدادی ساطع کننده مجزا در نظر گرفته شود که در همان صفحه جاگذاری ساکشن های خالء قرار بگیرد حتما باید دقت شود که صفحه از مواد نارسانایی مانند پلی اتیلن، تفلون،
UHMW، PVC یا آکریلیک ساخته شود.
هر جزء بازوی روبوتیک که در مجاورت اعمال کننده قرار دارد، در صورت عدم از دست
دادن استحکام و یکپارچگی بهتر است از مواد نارسانا ساخته شود. هر جزء فلزی یا رسانا هم باید به زمین )الکتریکی( متصل شود.
برای انتخاب نوع اعمال کننده شارژر دو انتخاب وجود دارد: جریان محدود و جریان نامحدود. اعمال کننده های جریان محدود در فرم یک میله استاتیکی مستقیم یا مجموعه ای از ساطع کننده های مجزا عرضه می شود و دربردارنده یک مقاومت است که با منبع تغذیه ولتاژ باال سری شده است.
مزیت استفاده از این نوع اعمال کننده، عدم بروز قوس الکتریکی شدید در صورت نزدیکی با فلز و کم خطر بودن آن در صورت تماس اتفاقی با بدن انسان است. در صورتی که اعمال کننده جریان نامحدود، به مواد فلزی مثل محفظه قالب خیلی نزدیکی شود، یا اینکه ولتاژ شارژ خیلی باالیی داشته باشد، جرقه می زند. حفره های ایجاد شده در اثر قوس الکتریکی درنهایت موجب خوردگی سطح قالب و عدم کارایی آن می شود.
بعضی از منبع تغذیه های پیشرفته تر مجهز به مدار تشخیص دهنده قوس الکتریکی است. در صورتی که شرایط شلک گیری قوس الکتریکی وجود داشته باشد، این مدار برای حفاظت خود در برابر اضافه بار، ولتاژ خروجی منبع تغذیه را قطع و یا محدود می کند. با استفاده از اعمال کننده جریان محدود، منبع تغذیه دچار اضافه بار نمی شود و در عین حال به بهترین وجه قادر به شارژ بی وقفه برچسب ها با بار الکترواستاتیکی است.
کابل رابط میان منبع تغذیه و اعمال کننده شارژر جریان الکتریکی، ولتاژ باالیی را منتقل می کند؛ به همین علت الزم است طول کافی داشته باشد تا در طول بازوی روبوت و در حین حرکات انجام شده دچار کشیدگی یا تنش فیزیکی احتمالی نشود. کابل مذکور باید هر هفته مورد بازبینی قرار گیرد و در صورت مشاهده شکستگی، سائیدگی یا ضعف تعویض شود.
روش ساده نصب با فاصله اعمال کننده شارژر نصب با فاصله اعمال کننده شارژر، روش ساده ای برای باردار کردن برچسب است. استفاده از این روش تنها به اعمال تغییرات جزئی در بازوی روبوتیک نیاز دارد، راه اندازی آن ساده است و به کمک آن می توان با استفاده از یک اعمال کننده شارژر، برچسب هایی با اندازه و شلک های گوناگون را به نحو مطلوب بارگذاری کرد.
دستگاه اعمال کننده روی ادوات بین پرس قالب گیری و صفحه برچسب ها نصب می شود. ادوات انتهای بازوی روبوتیک شامل یک صفحه فلزی رسانا است. این صفحه رسانا باید الاقل به اندازه برچسب باشد و با فاصله ۶/۳۵ تا ۱۲/۷میلی متر، مستقیما پشت برچسب قرار داشته باشد.
قطر دریچه های ساکشن خالء باید به اندازه ای باشد که قدرت مکندگی کافی داشته و از لغزیدن و جذب برچسب به صفحه رسانا که نقش زمین را بازی می کند، جلوگیری نماید. همه اجزاء رسانای تجهیزات نصب شده در انتهای بازوی روبوتیک باید به زمین متصل باشد )زمین الکتریکی( و فاقد لبه یا کنج تیز باشد. باید دقت شود تا فاصله یک اینچی برچسب، هیچ لبه یا کنج تیزی وجود نداشته باشد.
در فرآیند مذکور ابتدا روبوت برچسب را از صفحه برچسب ها جدا می کند، جهت آن را مشخص می نماید و آن را در محل بارگذاری قرار می دهد. سطح فلزی پشت برچسب که نقش زمین الکتریکی را دارد، انرژی میدان الکتریکی تولید شده توسط میله دستگاه اعمال کننده را جذب می کند و موچب باردار شدن برچسب می شود.
سپس روبوت برچسب را در محل مورد نظر از سطح محفظه قالب قرار می دهد و دریچه های ساکشن خالء برچسب را رها می کند؛ برچسب سر جای خود ثابت باقی می ماند. برچسب باردار شده می تواند، موجب باردار شدن سطح دریچه ها شود و ایجاد جذب الکترواستاتیکی شود.
در این صورت ممکن است برچسب به راحتی از دریچه ها جدا نشود یا اینکه هنگام جدا شدن از جهت مشخص شده، اندکی انحراف پیدا کند. برای رفع این مشلک، می توان از میله خنثی کننده بار الکترواستاتیکی استفاده کرد. هر بار که روبوت برای برداشتن برچسب جدید به صفحه برچسب ها رجوع می کند با استفاده از این میله دریچه های ساکشن از هرگونه بار الکتریکی احتمالی تخلیه می شود.
دریچه های کوچک تر به علت سطح کوچکتر کمتر باردار می شود و به این ترتیب با استفاده از دریچه های کوچکتر مشلک فوق الذکر کمتر می شود.
برای اینکه انتقال برچسب از تجهیزات نصب شده در بازوی روبوتیک به محفظه قالب راحت تر و بدون بروز مشکالت فیزیکی صورت گیرد، از یک قطعه فوم الکترواستاتیک استفاده می شود. این قطعه فوم به صفحه فلزی انتهای بازروی روبوتیک که پشت برچسب قرار دارد، چسانده شده است.
این قطعه فوم باید ضخامتی در حدود ۸/۳ اینچ داشته و مقاوت سطحی وحجمی آن در حدود ۱۰^۹ تا ۱۰^۱۰ اهم باشد. سطح اکثر مواد ضد استاتیکی تولید شده دندانه دار و ناهموار است و برای صاف و یکدست شدن باید سمباده زده شود. سمباده زدن سطح فوم ضد استاتیک میزان باردار شدن برچسب را نیز افزایش می دهد.
دریچه های ساکشن خالء توسط فوم ضد استاتیکی احاطه شده است و باید سطح آنها با سطح فوم تراز شده باشد. تصویر زیر نحوه عملکرد این روش را نشان می دهد. از آن جایی که الیه فوم در مقایسه با سطح فلزی محفظه قالب مقاومت الکتریکی باالیی دارد، برچسب تمایل به جذب به سطح محفظه قالب دارد. به این ترتیب به محض اینکه پمپ خالء خاموش شود و مکندگی دریچه های ساکشن متوقف شود، برچسب از روی فوم به سطح محفظه قالب منتقل می شود.
در طراحی بازوی روبوتیکی که اعمال کننده شارژر را درون خود جای می دهد باید چند نکته را مد نظر قرار داد. چون بخش ساطع کننده اعمال کننده باید ۱ اینچ از برچسب فاصل داشته باشد، حتما الزم است هر جزء فلزی بازوی روبوتیک به زمین )الکتریکی(متصل شود و الاقل ۱/۵ اینچ از بخش ساطع کننده فاصله داشته باشد.
هر جزء فلزی که فاصله ای کمتر از ۱/۵ اینچ تا ساطع کننده داشته باشد بخشی از میدان الکترواستاتیکی تولید شده توسط اعمال کننده را به خود جذب می کند و موجب می شود برچسب الکتریسیته ساکن کمتری پیدا کند. اگر در طراحی بازوی روبوتیک تعدادی ساطع کننده مجزا در نظر گرفته شود که در همان صفحه جاگذاری ساکشن های خالء قرار بگیرد حتما باید دقت شود که صفحه از مواد نارسانایی مانند پلی اتیلن، تفلون،
UHMW، PVC یا آکریلیک ساخته شود. هر جزء بازوی روبوتیک که در مجاورت اعمال کننده قرار دارد، در صورت عدم از دست دادن استحکام و یکپارچگی بهتر است از مواد نارسانا ساخته شود. هر جزء فلزی یا رسانا هم باید به زمین )الکتریکی( متصل شود.
برای انتخاب نوع اعمال کننده شارژر دو انتخاب وجود دارد: جریان محدود و جریان نامحدود. اعمال کننده های جریان محدود در فرم یک میله استاتیکی مستقیم یا مجموعه ای از ساطع کننده های مجزا عرضه می شود و دربردارنده یک مقاومت است که با منبع تغذیه ولتاژ باال سری شده است.
مزیت استفاده از این نوع اعمال کننده، عدم بروز قوس الکتریکی شدید در صورت نزدیکی با فلز و کم خطر بودن آن در صورت تماس اتفاقی با بدن انسان است. در صورتی که اعمال کننده جریان نامحدود، به مواد فلزی مثل محفظه قالب خیلی نزدیکی شود، یا اینکه ولتاژ شارژ خیلی باالیی داشته باشد، جرقه می زند.
حفره های ایجاد شده در اثر قوس الکتریکی درنهایت موجب خوردگی سطح قالب و عدم کارایی آن می شود. بعضی از منبع تغذیه های پیشرفته تر مجهز به مدار تشخیص دهنده قوس الکتریکی است. در صورتی که شرایط شلک گیری قوس الکتریکی وجود داشته باشد،
این مدار برای حفاظت خود در برابر اضافه بار، ولتاژ خروجی منبع تغذیه را قطع و یا محدود می کند. با استفاده از اعمال کننده جریان محدود، منبع تغذیه دچار اضافه بار نمی شود و در عین حال به بهترین وجه قادر به شارژ بی وقفه برچسب ها با بار الکترواستاتیکی است.
کابل رابط میان منبع تغذیه و اعمال کننده شارژر جریان الکتریکی، ولتاژ باالیی را منتقل می کند؛ به همین علت الزم است طول کافی داشته باشد تا در طول بازوی روبوت و در حین حرکات انجام شده دچار کشیدگی یا تنش فیزیکی احتمالی نشود.
کابل مذکور باید هر هفته مورد بازبینی قرار گیرد و در صورت مشاهده شکستگی، سائیدگی یا ضعف تعویض شود.
روش ساده نصب با فاصله اعمال کننده شارژر نصب با فاصله اعمال کننده شارژر، روش ساده ای برای باردار کردن برچسب است.
استفاده از این روش تنها به اعمال تغییرات جزئی در بازوی روبوتیک نیاز دارد، راه اندازی آن ساده است و به کمک آن می توان با استفاده از یک اعمال کننده شارژر، برچسب هایی با اندازه و شلک های گوناگون را به نحو مطلوب بارگذاری کرد.
دستگاه اعمال کننده روی ادوات بین پرس قالب گیری و صفحه برچسب ها نصب می شود. ادوات انتهای بازوی روبوتیک شامل یک صفحه فلزی رسانا است. این صفحه رسانا باید الاقل به اندازه برچسب باشد و با فاصله ۶/۳۵ تا ۱۲/۷میلی متر، مستقیما پشت برچسب قرار داشته باشد.
قطر دریچه های ساکشن خالء باید به اندازه ای باشد که قدرت مکندگی کافی داشته و از لغزیدن و جذب برچسب به صفحه رسانا که نقش زمین را بازی می کند، جلوگیری نماید. همه اجزاء رسانای تجهیزات نصب شده در انتهای بازوی روبوتیک باید به زمین متصل باشد )زمین الکتریکی( و فاقد لبه یا کنج تیز باشد. باید دقت شود تا فاصله یک اینچی برچسب، هیچ لبه یا کنج تیزی وجود نداشته باشد.
در فرآیند مذکور ابتدا روبوت برچسب را از صفحه برچسب ها جدا می کند، جهت آن را مشخص می نماید و آن را در محل بارگذاری قرار می دهد. سطح فلزی پشت برچسب که نقش زمین الکتریکی را دارد، انرژی میدان الکتریکی تولید شده توسط میله دستگاه اعمال کننده را جذب می کند و موچب باردار شدن برچسب می شود.
سپس روبوت برچسب را در محل مورد نظر از سطح محفظه قالب قرار می دهد و دریچه های ساکشن خالء برچسب را رها می کند؛ برچسب سر جای خود ثابت باقی می ماند. برچسب باردار شده می تواند، موجب باردار شدن سطح دریچه ها شود و ایجاد جذب الکترواستاتیکی شود.
در این صورت ممکن است برچسب به راحتی از دریچه ها جدا نشود یا اینکه هنگام جدا شدن از جهت مشخص شده، اندکی انحراف پیدا کند. برای رفع این مشلک، می توان از میله خنثی کننده بار الکترواستاتیکی استفاده کرد. هر بار که روبوت برای برداشتن برچسب جدید به صفحه برچسب ها رجوع می کند با استفاده از این میله دریچه های ساکشن از هرگونه بار الکتریکی احتمالی تخلیه می شود.
دریچه های کوچک تر به علت سطح کوچکتر کمتر باردار می شود و به این ترتیب با استفاده از دریچه های کوچکتر مشلک فوق الذکر کمتر می شود. برای اینکه انتقال برچسب از تجهیزات نصب شده در بازوی روبوتیک به محفظه قالب راحت تر و بدون بروز مشکالت فیزیکی صورت گیرد، از یک قطعه فوم الکترواستاتیک استفاده می شود.
این قطعه فوم به صفحه فلزی انتهای بازروی روبوتیک که پشت برچسب قرار دارد، چسانده شده است. این قطعه فوم باید ضخامتی در حدود ۸/۳ اینچ داشته و مقاوت سطحی وحجمی آن در حدود ۱۰^۹ تا ۱۰^۱۰ اهم باشد. سطح اکثر مواد ضد استاتیکی تولید شده دندانه دار و ناهموار است و برای صاف و یکدست شدن باید سمباده زده شود. سمباده زدن سطح فوم ضد استاتیک میزان باردار شدن برچسب را نیز افزایش می دهد.
دریچه های ساکشن خالء توسط فوم ضد استاتیکی احاطه شده است و باید سطح آنها با سطح فوم تراز شده باشد.
نحوه عملکرد این روش را نشان می دهد. از آن جایی که الیه فوم در مقایسه با سطح فلزی محفظه قالب مقاومت الکتریکی
باالیی دارد،
برچسب تمایل به جذب به سطح محفظه قالب دارد. به این ترتیب به محض اینکه پمپ خالء خاموش شود و
مکندگی دریچه های ساکشن متوقف شود، برچسب از روی فوم به سطح محفظه قالب منتقل می شود.
آینده روشن برای بسته بندی
IML
هم اکنون تقاضای باالیی برای برچسب های ترکیبی در بازار IML وجود دارد و این تقاضا رو به افزایش است. گذر از برچسب های
کاغذی به فیلم های ترکیبی چندین سال است که آغاز شده و پیش بینی می شود در آینده نیز ادامه یابد. فیلم های ترکیبی
معادل ۸۰ درصد )
ارزش دالری( بازار IML را به خود اختصاص داده اند و انتظار می رود استفاده از راه کار قالب گیری تزریقی طی
چند سال آینده بیشترین رشد این بازار در ایاالت متحده را به خود اختصاص دهد. فن آوری IML بخشی از رشد خود را مرهون
مباحث زیبایی شناختی است؛
عرضه کنندگان کاال برای اطمینان از رساندن پیام خود به مصرف کننده، نیازمند برچسب های زیباتر
و تأثیرگذار تر هستند؛ تا زمانی که این تقاضا وجود داشته باشد بازار IML همچنان به رشد خود ادامه خواهد داد.
مزایای استفاده از ظروف IML سودی بسپار به شرح زیر می باشد :
آب بندی بودن کامل ظروف
کیفیت چاپ باال و شفافیت چشم نواز
مقاومت در برابر نفوذ هوا و مقاومت زیاد در برابر آلودگی
قابلیت انعطاف پذیری ظروف بطوریکه لیبل بخشی از ظرف می شود بنابراین ظرف می تواند خم شود،فشرده شود،
تغییر شلک
دهد بدون اینکه لیبل از آن جدا شود
این ظروف بدلیل دیواره نازک دارای وزن سبک تری هستند
با صرفه بودن قیمت لیبل و عدم نیاز به ماشین آالت لیبل زنی
سهولت در بسته بندی و عدم نیاز به ماشین آالت خاص درب بندی
مواد ولیبل استفاده شده
برای تولید این ظروف وقتی تبدیل به ظرف می شود از استحکام باالیی برخوردار بوده و این مسئله
باعث افزایش ماندگاری محصوالت بسته بندی شده با این ظروف می شود.
عدم آلوده شدن ظروف هنگام تولید و بسته بندی به علت استفاده از ربات های ویژه
دستاندرکاران صنعت پالستیک به موازات خانواده چاپ در تجهیز امکانات و ارتقای قابلیتهای خود کوشیدند و به تدریج
پتانسیل خوبی در کشور ایجاد شد که البته هنوز هم از سطح تقاضا عقبتر بود. در بحثهای فنی و تخصصی که به ویژه در زمینه چاپ و تولید لیبل IML صورت میگرفت، مشکالت چاپی قابل حل به نظر میرسید و مدیران چند چاپخانه نیز از
پیشرفتهای خود در این زمینه سخن میگفتند.
ولی مشکلی که تا همین اواخر الینحل ماند- و هنوز هم خبری موثق درباره باز شدن گره کور آن شنیده نشده- دایکات و ساخت قالب برش لیبلها بود. به هر حال تا دو سال گذشته این نامها در عرصه تولید ظروف IML مطرح بودند:
– ایحا گستر شمال
– پایا پالست زرین
– پترو پالستیک تبریز
– پلیمر پک پارس
– پیکره
– تهران تولید
– رمزینه برچسب
– فرسگال پالست
– کرد پلیمر
اما طی یکی دو سال اخیر سرمایه گذاری هایی در این رشته صورت گرفته و آن طور که از آگهی ها و اعلان های چاپ شده در نشریات چاپ و بسته بندی دریافت می شود، شرکت های فعال و تازه نفسی در رشته IML پا به میدان گذاشته اند:
– آوند پالستیک مشهد
– رز پالستیک تهران
– صدرا جام پالست تهران
– نیکان پالستیک کرمانشاه
– شرکت نفت سپاهان اصفهان
IML در اصل از فرآیند )Decoration Mold In (IMD گرفته شده است. شما در فرآیند IMD قطعه را در داخل قالب قرار داده و روی آن فرایند تزریق را انجام میدهید. IMD برای قطعات مختلف در گوشی تلفن همراه، قطعات الکترونیکی، قطعات اتومبیل، قطعات تزئینی، لوازم خانه و … کاربرد دارد. تصویر یا برند مد نظرتان را در قالب میگذارید و به وسیله تزریق پالستیک آن را روی قطعه ماندگار میکنید.
برای IML پس از چاپ و دایکات لیبل، آن را به وسیله پمپ مکش یا خالء )suction -)که فشار مکش آن به اندازهای تنظیم شده است که تنها یک لیبل را بردارد- لیبل را برداشته و در دیواره قالب قرار میدهید. برای ثابت نگه داشتن لیبل در دیواره قالب دو راه وجود دارد: یا استفاده از شارژ الکترواستاتیک و یا مکش.
البته ترکیبی از هر دو روش نیز ممکن است. پس از قرار گرفتن لیبل باید فرآیند تزریق هماهنگ با آن انجام شود. به نظر من مهمترین قسمت کار و به نوعی گلوگاه کار، هماهنگی دستگاه با ربات، ربات با قالب و قالب با قسمتهای دیگر است.
باید دستگاه طوری طراحی شود که قطع و وصل شدن، به حداقل برسد. چون اگر قسمتی از سیستم مشلک داشته باشد یا با بقیه قسمت ها هماهنگ نباشد، لک خط تولید میخوابد و این ضرر بزرگی محسوب میشود. مشکالت تولید IML برای صنایع مختلف کدامند؟
یکی از مشکالت تولید IML تعداد حفرههای )Cavity )پایین سیستم تزریق و زمانبر بودن سیلک تولید است. تعداد نرمال و معمول حفرهها برای IML بین ۲ تا ۴ است، چون هر چقدر تعداد حفرهها باالتر برود، حجم دستگاه باید بزرگتر شود و
پیچیدگیهای سیستم در قسمت رباتها و کنترلکنندهها سخت میشود. ضمن اینکه اگر خطایی در فرآیند رخ دهد، امکان
تشخیص آن سختتر میشود و دیرتر به خطا پی میبریم.
چون برای این فرآیند باید کامال ظروف را دید تا مشکلی وجود نداشته باشد، زمان سیلک تولید برای ظروف IML بین ۳ تا ۴ ثانیه برای ظروف سبک و کم حجم و کوچک و ۱۵ تا ۳۰ ثانیه برای ظروف ۵ تا ۱۰ کیلوگرمی است.
هماهنگی بین طراحی ربات، رباتساز، قالبساز و ماشینساز میتواند سیلک تولید را به حداقل برساند.
االن برای نصب این دو دستگاه ما سرمایهگذاری بالغ بر یک میلیارد تومان الزم است و میتوان از آنها انتظار تولید ۲۰ تا ۴۰ هزار ظرف IML را در شبانهروز داشت. شما حساب کنید این برای صنایع لبنی که تیراژ کارشان باالست، عدد قابل مالحظهای محسوب نمی شود.
االن قفسههای سوپر مارکت بیشتر کشورها، مملو از ظروف IML است و لیبلهای قدیمی در حال برچیده شدن است.
در کشور ما IML مثل پریفورم است که به مرور جا افتاد. فکر میکنم صنعت IML هم تا ۶-۵ سال آینده جای خود را در کشور باز کند و قفسههای سوپرمارکتها را تصرف کند.
زیرا IML یک تبلیغ دایمی است و کیفیت آن قابل کپیبرداری نیست و نیز میتوان با هزینه کمی، برند و کپیرایت را محافظت کرد.
وضعیت تولید IML در ایران
ایران بزرگترین بازار مصرف ظروف تزریقی پالستیکی IML در خاورمیانه پس از ترکیه و عربستان سعودی است و عالوه بر واردات گسترده این قبیل ظروف از خارج کشور، تعدادی از شرکتهای داخلی نیز اقدام به تولید در داخل کشور کرده اند.
شرکتهای فرسگال پالست، پاک تاب مروارید، کردپلیمر، پیکره، پلیمرپاک، بناالکترونیک پارس، ایحاگسترشمال، پلیمرپالست، پاک آوندلیا، ماهان پالست زنجان، پتروپالست زنجان و صدراجم پالست از جمله تولیدکنندگان داخلی هستند که بیش از ۴۰۰ میلیون انواع ظروف IML در سال ۱۳۹۰ تولید کردهاند.
بالغ بر ۳۰۰ میلیون قطعه ظرف IML آماده مصرف نیز وارد کشور شده که مبدا بیشتر آنها کشورهای اروپایی از جمله ترکیه است.
رشد بازار مصرف لیبلهای IML در جهان برابر آمار AWA بیش از ۵ درصد برای سال ۲۰۱۲ پیشبینی شده بود در ایران با توجه به آمار نصب ماشینآالت تزریق مخصوص و تقاضای باالی بازار، مصرف لیبلهای مذکور ۱۸ درصد در سال ۱۳۹۰ رشد داشت و تقاضای بازار ۱۶ درصد در سال ۱۳۹۱ نسبت به سال قبل بیشتر شد و از مرز ۷۰۰ میلیون قطعه فراتر رفت.
در ایران همه تولیدکنندگان ظروف پالستیکی IML لیبلهای مورد نیازشان را از خارج کشور تهیه میکنند، زیرا تجهیزات مخصوص دایکات
لیبلهای IML در ایران وجود ندارد.
فرایند تولید ظروف و لیبلهای IML
همانطور که اشاره شد فناوری لیبلچسبانی در قالب یا IML از جمله روشهای پرطرفدار الصاق لیبل به ظروف پالستیکی است. در این روش لیبلهای چاپ شده از جنس فیلم PP شفاف و صدفی، پس از چاپ و دایکات در اشکال معین و متناسب با ظرف با استفاده از روبوت از داخل خشاب خارج شده و داخل قالب قبل از تزریق پلیمر به کمک القای بار الکتریکی یا کانالهای خالء جایگذاری و ثابت میشوند.
با تزریق مواد مذاب پالستیکی به داخل قالب، لیبل و ظرف پالستیکی یکپارچه میشوند و به هیچ وجه نمیتوان لیبل را از بدنه ظرف جدا کرد. جایگذاری لیبل و ثابت کردن آن درون قالب در صورتی که با اشکال مواجه شود، منجر به تولید ظروف معیوب با لیبل چروک و ناصاف یا نفوذ مواد مذاب به داخل مجاری مکنده لیبل میشود.
از همین روش با اندکی تغییرات در فنآوریهای molding Blow و Thermoforming نیز استفاده میشود. کیفیت لیبل از وجوه مختلف )نوع و ضخامت فیلم، نوع مرکب و پوشش ورنی، کیفیت چاپ و دایکات، کیفیت بستهبندی لیبلها برای سهولت انتقال به خشاب دستگاه و …( برای تولیدکنندگان ظروف IML اهمیت بسیار باالیی دارد. از این رو آنها در انتخاب تولیدکننده لیبلهای
IML حساسیت ویژهای به خرج میدهند، چرا که هر گونه اشکال به هنگام عملیات لیبلگذاری از خشاب تا قالب، منجر به افت کمی تولید و حتی توقف ماشین میشود.
مواد مصرفی، چاپ و دایکات
چاپ لیبلهای IML با استفاده از انواع ماشینهای چاپ رول و ورقی و با استفاده از مرکبهای معمولی و UV امکانپذیر است. البته استفاده از مرکبهای UV از نوع Migration Low برای این نوع لیبلها مانند همه لیبلهای مورد استفاده در صنایع غذایی توصیه میشود. )ذکر این نکته ضروری است که اغلب مرکبهای UV مورد استفاده در صنعت چاپ ایران از نوع Migration Low نیستند،
بنابراین به علت نفوذ مرکب در محصول بستهبندی شده، برای استفاده در چاپ لیبلهای مواد غذایی زیانآورند. اما متاسفانه به علت تفاوت قیمت ۲۰ درصدی بعضی از چاپخانهداران به این نکته توجه نمیکنند.
( اما روش چاپ و دایکات رول به واسطه کاهش هزینههای تولید، بیشتر مورد استفاده قرار میگیرد. افست، فلکسو، گراوور و حتی دیجیتال از تکنیکهای مورد استفاده در چاپ لیبلهای IML است و میتوان متناسب با تیراژ از هر یک بهره گرفت. همچنین میتوان پس از چاپ، از پوشش ورنی مناسب)Contact Food )استفاده کرد.
دایکات و دسته کردن لیبلهای IML به علت حساسیتهای خاص و لزوم دوری از هرگونه گرد و غبار و الکتریسته ساکن و کیفیت برش لبههای لیبل، حساسترین قسمت فرایند تولید این لیبل هاست. برای دایکات لیبلهای چاپ شده نیز از تکنیکهای گوناگون دایکات رول و ورقی استفاده میشود.
لیبلهای IML میبایست در یک مرحله به صورت کامل دایکات و پوشالبرداری شوند. لذا پس از تیغ زدن کامل لیبلهای چاپ شده، تماس لیبلها با حواشی بهطور کلی قطع میشود و امکان سوسه زدن به هیچ وجه وجود ندارد. به بیان دیگر پس از تماس تیغ با متریال، لک حواشی برش شده و لیبل رها میشود و باید بالفاصله دسته شود )
در ماشینهای دایکات تخت( یا با استفاده از نقالههای مکنده )Conveyer Vacuum )به سمت دستهکن )Stacker )در ماشینهای دایکات رول هدایت شود. در میان انواع فناوریهای دایکات لیبلهای IML ،دایکات روتاری با استفاده از تیغهای دایکات انعطافپذیر )Dies Flexible )مقرون به صرفهترین است، چرا که
قالبهای دایکات تخت و نر و ماده در مقایسه با تیغهای دایکات انعطافپذیر قیمت باالتری دارند. ماشینهای دایکات روتاری با سرعت ۱۰۰ متر در دقیقه لیبلهای IML چاپ شده از جنس فیلم پلی پروپیلن و ضخامت ۴۰ تا ۱۰۰ میکرون را دایکات و دسته میکنند.
از شرکتهای تولیدکننده ماشین برای دایکات لیبلهای IML میتوان به Blumer-Bosch-Kemec-Remele-Berhalter اشاره کرد، ولی قالب تیغ آنها از نوع نر و ماده بوده و محدودیت سایز در تولید لیبل دارند. عالوه بر شرکت Bobst با فناوری قالب دایکات تخت و پوشالگیری همزمان، شرکتهای Heidelberg و Schober نیز اقدام به تولید ماشینهای دایکات روتاری XL۱۰۵DD و
RSM برای لیبلهای IML کردهاند. در ماشینهای دایکات رول Schober لیبلهای ابعاد بزرگ با استفاده از روبوت پس از دایکات از روی نقاله برداشته و داخل کارتن قرار میگیرند. این اقدام در کیفیت تولید و بستهبندی لیبلها بدون القای کوچکترین بار الکتریکی موثر است.
تولید لیبلهای IML در ایران
بازار لیبلهای IML ایران در دست چاپخانههای ترکیهای است. بیش از ۸ میلیون یورو انواع لیبل IML در سال ۱۳۹۰ فقط از ترکیه وارد ایران شده و شرکتهای چاپ ترکیهای بیشترین سهم را در تولید لیبلهای IML برای شرکتهای ایرانی دارد.
اگر چه امکان چاپ این نوع لیبلها در ایران با استفاده از ماشینهای چاپ رول و ورقی افست و فلکسو وجود داشته و مدعیان بسیاری دارد، ولی به علت فقدان دانش فنی تولید یا دستگاه دایکات مخصوص، هنوز هیچ یک از شرکتهای داخلی موفق به تولید این نوع لیبل ها در ایران نشده اند و از این رو در نمایشگاه بینالمللی چاپ و بسته بندی تهران طی سالهای اخیر بسیاری از چاپخانه های لیبل ترکیهای حضور فعالی داشتهاند.
ذکر این نکته ضروری است که علی رغم تجهیز یکی، دو چاپخانه ایران به دستگاه های دایکات ورقی مخصوص با قابلیت دایکات لیبلهای IML و حاشیه سود به مراتب فراتر از دایکات جعبههای سیگار، پودر و دارو، هنوز این چاپخانهها اقدامی برای تولید لیبلهای IML نکردهاند. تولید تگها و پاکتهای چای کیسهای در ایران هم داستانی شبیه به لیبلهای IML دارند.
شرکتهای تولید و بستهبندی چای در ایران بیش از ۷ میلیارد بسته چای کیسه ای در سال ۱۳۹۰ تولید کرده اند. اغلب تگ های مورد استفاده در چای های کیسه ای مورد استفاده در ایران وارداتی اند. چرا که چاپخانه های لیبل ایران توانایی دایکات مخصوص این نوع تگها با کیفیت مطلوب را ندارند.
ارزش واردات این تگهای مقوایی در سال ۱۳۹۰ حدود۵ میلیارد تومان برآورد میشود. همچنین برخی از پاکت های مخصوص بسته بندی چای کیسهای به علت شلک ویژه و نیاز به دایکات هم قابلیت تولید در کشور را ندارند اما نیمی دیگر که به صورت نوار چاپ شده و به صورت رول به رول برش میشوند، خاص ایران و توسط چاپخانههای چاپ لفاف، تولید میشوند.
کشورهای سریالنکا، ترکیه، امارات و هند بزرگترین صادرکنندگان تگ و پاکت چای کیسهای به شرکتهای یونیلور ایران، چای احمد، گلستان، بهنوش، فومن، طال و … هستند. در کنار واردات این نوع تگها برای چای کیسهای، در سال ۱۳۹۰ بیش از یک میلیارد تومان انواع بلیطهای مقوایی مخصوص دستگاههای شهر بازی هم وارد کشور شده که این محصول هم به واسطه دایکات خاص قابلیت تولید در ایران را ندارد.
مراحل تولید ظروف پلاستیکی
ظروف پلاستیکی به دو روش تولید می شوند که عبارتند از :
تولید ظروف پلاستیکی با سیستم تولید نیمه فرمینگ
تولید ظروف پلاستیکی با سیستم تولید ترموفرمینگ
تولید ظروف پلاستیکی با سیستم نیمه فرمینگ
در این روش تمامی فرآیند تولید در یک دستگاه انجام می شود .
مواد اولیه به شکل گرانول پتروشیمی در قسمتی از خط تولید
که اکسترودر نامیده میشود ، ذوب و تبدیل به ورق گرم شده
و قبل از سرد شدن ورق البته با توجه به نوع و امکانات دستگاه این ورق ،
بدون نورد و یکنواخت شدن ، ورق گرم وارد قسمت پرس شده
و در زیرقالب عملیات فرم دهی و تولید ظروف پلاستیکی انجام می پذیرد .
تولید ظروف پلاستیکی با سیستم ترموفرمینگ
در این روش فرآیند تولید برخلاف روش نیمه فرمینگ ، شامل دو دستگاه بوده
که در دستگاه اول مواد اولیه بصورت گرانول به ورق تبدیل و به صورت رول تولید می شود
ودر دستگاه دوم که به نام پرس ترموفرمینگ می باشد ورق آماده تولید شده
با عبوراز کوره حرارتی و رسیدن به درجه حرارت لازمه برای فرم گیری
وارد قسمت پرس شده و درزیرقالب عملیات تولید ظروف انجام می پذیرد .
هزینه های خط تولید ظروف پلاستیکی
هزینه ی سرویس دستگاه ها
هزینه ی خرید مواد اولیه
دستمزد و هزینه های مربوط به نیروهای انسانی
هزینه ی اجاره یا خرید مکان خط تولید
هزینه های آب ، برق و گاز
سود و درآمد خط تولید ظروف پلاستیکی
اگر قصد ایجاد خط تولید ظروف پلاستیکی را دارید ، باید به شما بگوییم
که سود و درآمد شما به عوامل مختلفی بستگی دارد مثلا از این عوامل می توان
به کیفیت محصولات و بازار یابی شما اشاره کرد . اگر بخواهید از این کسب و کار
، سود به دست آورید باید درآمد شما به گونه ای باشد که علاوه بر پرداخت
تمامی هزینه های فوق بازهم برای شما چیزی باقی بماند .
مواد تشکیل دهنده ظروف پلاستیکی
در خط تولید ظروف پلاستیکی از مواد پلیمری مختلفی استفاده می شود .
به عنوان مثال : ظروف نوشابه های گازدار از جنس پلی اتیلن تترافتالات است
، شیشه های شیر کودکان از پلی کربنات PVC ساخته می شوند .
مواد اولیه ظروف بسته بندی لبنیات را جنس پلیاتیلن (PE)،
پلیپروپیلن (PP) و پلیاستایرن (PS) تشکیل میدهند .
در ساخت ظروف یکبارمصرف از مواد پلیپروپیلن PP و پلیاستایرن PS نیز استفاده میشود .
ظروف پلاستیکی انواع مختلف دارند و هر کدام از آن ها یک کاربردی دارند .
از آن جایی که مواد به کار رفته در هر نوع خاص از ظروف پلاستیکی با یک دیگر متفاوت است ،
بنابراین هر نوع از ظروف پلاستیکی ، مناسب برای استفاده ای خاص است .
به عنوان مثال : ظروف پلاستیکی بی رنگ و شفاف ، فقط برای غذاها
و نوشیدنی های سرد مناسب هستند . ظروف یکبارمصرف سفید
و فوم دار برای موادغذایی سرد ، گرم (با دمای پایین حدود ۶۵ درجه سانتیگراد)
و مرطوب مناسب هستند .
معایب ظروف پلاستیکی
اگر بخواهیم معایب ظروف پلاستیکی را با ظروف کاغذی مقایسه کنیم ،
ظروف کاغذی از آن جایی که از جنس طبیعی هستند ، هیچ آسیبی به محیط زیست وارد
نمی کنند ، این ظروف بعد از ورود به محیط زیست ، توسط خاک تجزیه می شوند
و مواد آن ها به چرخه خاک باز می گردند .
اما مشکل بزرگ و اساسی ظروف پلاستیکی
آن است که این ظروف از موادی تشکیل شده اند که همگی تجذیه ناپذیر هستند ،
بنابراین دولت و به خصوص شهرداری ها ، برای از بین بردن این مواد ، با مشکلات زیادی
روبه رو می شوند هم چنین مجبور به صرف هزینه های گزاف خواهند شد .
بنابراین شاید راه اندازی خط تولید ظروف پلاستیکی و سرمایه گذاری در این بخش ،
سودآوری مناسب و هم چنین توجیه اقتصادی نداشته باشد .
امروزه یکی از بیش ترین کاربرد های ظروف یکبار مصرف ،
در رستوران ها و فست فود ها
می باشد اما به هیچ عنوان جنس این ظروف یکبار مصرف را از پلاستیک نمی زنند ،
زیرا غذاها داغ هستند و استفاده از ظروف پلاستیکی برای غذاهای داغ اصلا مناسب نیست .
دستگاه های مورد نیاز جهت ایجاد خط تولید ظروف پلاستیکی
اغلب دستگاه های ساخت ظروف پلاستیکی ، ساخت کره و چین هستند و به صورت استوک
در بازار موجود می باشند و قیمت های متفاوتی دارند . بسیاری از کارخانجات ایران
به دلیل داشتن ماشین آلات نیمه فرمینگ ، قابلیت تولید ظروف فقط از مواد پلی استایرن را دارند
اما تعداد انگشت شماری از تولیدکنندهها اقدام به خرید ماشینآلات مدل جدید
و تولید ظروف یکبارمصرف با سیستم ترموفرمینگ کردهاند .
ماشین آلاتی که در خط تولید ظروف پلاستیکی ، وجود دارند در زمره ی
دستگاه های صنعتی نسبتا گران قیمت قرار می گیرند .
از آن جایی که امروزه سرمایه های مالی ، محدود هستند ،
بسیاری از سرمایه گذارانی که قصد راه اندازی خط تولید ظروف پلاستیکی را دارند ، توان مالی کافی برای خرید دستگاه های مورد نیاز را ندارند .
قیمت دستگاه های مورد نیاز جهت راه اندازی خط تولید ظروف پلاستیکی
دستگاه های مورد نیاز جهت راه اندازی خط تولید ظروف پلاستیکی
، دارای قیمت های متفاوتی هستند ، این قیمت ها بستگی به مواردی از قبیل
ساخت ایران یا وارداتی بودن ، چینی و یا اروپایی بودن برای دستگاه های اروپایی
، کیفیت قطعات به کار رفته در ساخت ماشین آلات ایرانی ، سرعت و ظرفیت تولید
، گارانتی و خدمات پس از فروش و مواردی از این دست دارد .
چگونه با یک انتخاب درست یک خط تولید به سود بالایی می توان رسید؟
بسیار مهم است که شما نسبت به خط تولیدی خود علاقه داشته باشید
و با تمام توان خود برای چندین برابر کردن سرمایه خود تلاش کنید اما سرمایه گذاری
در هر خط تولید نیز پیشنهاد نمی شود چرا که ممکن است بدون فکر عمل کردن
همان سرمایه اولیه را از شما ببرد . شما می توانید با مشاورین شرکت سارگن استون تماس
بگیرید و در رابطه با انواع خطوط تولیدی پیشنهادی این شرکت از آن ها کمک بگیرید
و از این طریق بهترین خط تولید را انتخاب کنید .
- خط تولیدی های پیشنهادی توسط سارگن استون :
- خط تولید ویلا و سوله پیش ساخته
- خط تولید سنگ گیوتینی و سنگ قیچی و سنگ جوشقان
- خط تولید سنگ نورانی و سنگ شبرنگ
- خط تولید نرده سنگی و صراحی سنگی و اشکال حجمی
- خط تولید سنگ جواهراتی و درمانی
- خط تولید سنگ قله و سنگ کوپ
- خط تولید سنگ ساب خور
- خط تولید دایموندگلس، وودگلس و جواهرات رزینی
- خط تولید سنگ طرح گل
- خط تولید سنگ اسلب نورانی
- خط تولید سنگ آنتیک و ابزار
- خط تولید سنگ مصنوعی پلیمری و سمنت پلاستیک
سایت B2wall امیدوار است که این مقاله برای شما کاربران عزیز کار امد باشد.
سلام
چرا خط تولید دستگاه قلب سازی پلاستیک انقدر رونق پیدا کرده؟
سلام
راه اندازی خط تولید دستگاه قالب سازی پلاستیک بسیار سود آور است چون با توجه به شیوه زندگی جدید صنعت پلاستیک به یکی از مهم ترین و پر کاربرد ترین صنایع تبدیل شده است به دلیل استفاده از محصولات پلاستیکی در صنایع مختلف می توان این صنعت را پایه بسیاری از صنایع دانست.
وقت بخیر
چه مواردی را باید برای راه اندازی خط تولید دستگاه قالب سازی پلاستیک در نظر گرفته شود؟
تحلیل محصول
تحلیل مواد اولیه
• فضای کارخانه
• مشاوره و ساخت قالب
• ماشین آلات
• تاسیسات
مهم ترین و سوداور ترین محصولات خط تولید دستگاه قالب سازی پلاستیک چیست؟
• سبد میوه.
• گلدان پلاستیکی.
• ظروف IML.
• جار.
• پریفرم.
• سپر و قطعات کوچک و بزرگ خودرو.
• میز و صندلی.
هزینه راه اندازی خط تولید دستگاه قالب سازی پلاستیک چقدر است؟
برای محاسبه راه اندازی خط تزریق پلاستیک فاکتورهای زیادی وجود دارد.
از جمله این فاکتورها در نظر گرفتن هزینهی مواد اولیه، هزینهی ماشین کاری و مدت زمانی است که باید صرف عملیات ساخت شود. منظور از ماشین کاری هزینهای است که قرار است صرف ساخت قالب شود.
ایا با استفاده از دستگاه خط تولید قالب سازی پلاستیک میتوان در صادرات هم سودی داشت؟
به علت تحریمات فعلا فقط به کشورهایی همسایه نظیر افغانستان و ترکیه صادرات ممکن است.
رایج ترین قطعات و ماشین آلات درقالب سازی پلاستیک چیست؟
سلام
1. دستگاه تزریق پلاستیک.
2. کنترل کننده قالب.
3. چیلر.
4. گازگیر.
5. موادکش.
6. آسیاب.
7. مخلوط کننده مواد (میکسر).
8. تجهیزات اتوماسیون.
وقت بخیر انواع دستگاه قالب سازی پلاستیک چیست؟
سلام
دستگاههای قالبگیری به ۳ دسته کلی هیدرولیکی ، برقی و هیبریدی تقسیم بندی میشوند
اجزای اصلی دستگاه قالب سازی پلاستیک چیست؟
سلام
دستگاه های تزریق پلاستیک از قیف تغذیه، مته مارپیچی و واحد حرارتی تشکیل شدهاند. در واقع قالبها در صفحات گیرهی دستگاه قفل شده و سپس پلاستیک از دهانه اسپرو به داخل قالب تزریق شده و در نهایت قطعه تزریقی ایجاد میشود
سلام قیمت دستگاه قالب سازی پلاستیک چقدر است؟
سلام
به علت نوسانات دلار قیمت دقیق و ثابتی برای محصولات نیست
برای اگاهی از قیمت محصولات به قسمت درخواست قیمت در سایت مراجعه کنید
سلام ایا برای دستگاه قالب سازی پلاستیک فروش اقساطی هم دارید؟
سلام بله