کوره ریخته گری چیست و 11 نوع آن
تاریخچه ریخته گری
کوره ریخته گری چیست؟
«ریخته گری» (Casting)، یکی از قدیمیترین فرآیندهای ساخت و تولید است که با ذوب مواد و ریختن آنها به درون قالب انجام میگیرد. این فرآیند، از متداولترین روشهای ساخت قطعات فلزی در صنایع مختلف به شمار میرود. کوره ریختهگری، امکان تولید انبوه قطعاتی با ابعاد کوچک تا بزرگ، وزن چند گرم تا چند تن، شکل ساده تا پیچیده و ساختار یکپارچه را فراهم میکند. روشهای متعددی برای اجرای ریخته گری وجود دارند. با این حال،کوره ریخته گری ماسه ای به عنوان قدیمیترین و رایجترین روش اجرای کوره ریختهگری شناخته میشود.
ویژگی های زیر می باشد:
– حداقل ناخالصی
– کاهش هیدروژن ذوب به کمتر از ppm 2.5
– کاهش نیتروژن ذوب به کمتر از ppm 50
– کاهش گوگرد ذوب به کمتر از% 0.007
– کاهش کربن ذوب به کمتر از% 0.03
– مقاومت به خوردگی بالا
– قابلیت جوشکاری بالا
– بهبود قابلیت ماشین کاری
– بهبود خواص مکانیکی
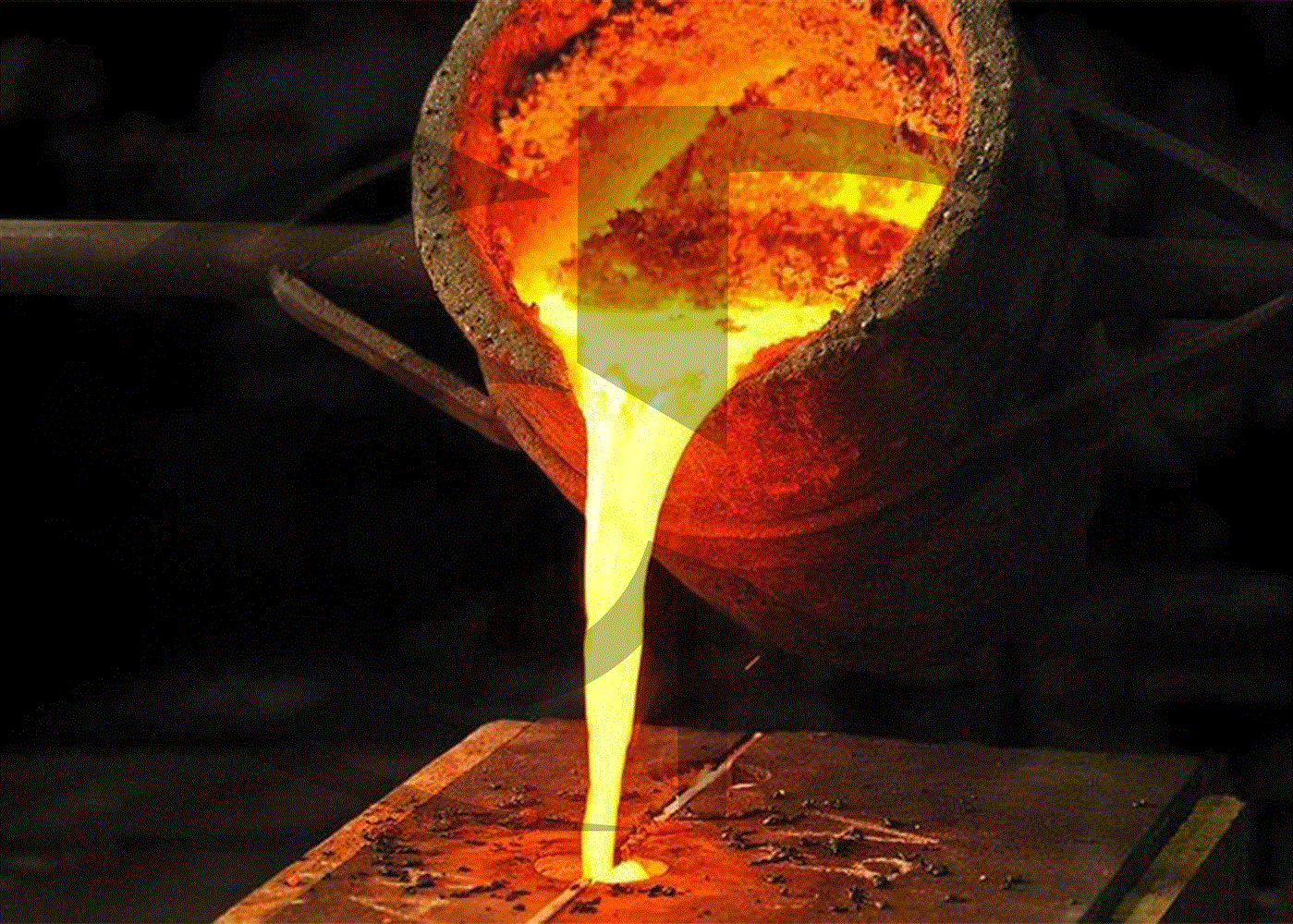
فرآیند ریخته گری یکی از روش های ساخت قطعات می باشد که در آن یک ماده (فلز) مذاب داخل یک قالب (شامل حفرۀ توخالی به شکل قطعۀ موردنظر) ریخته شده تا به مرور سرد و در نهایت قطعۀ نهایی از آن خارج گردد. از مزایای اصلی بکارگیری این روش می توان به تولید قطعه با پیچیدگی شکلی و ظاهری بالا و تولید انبوه در زمان کوتاه با هزینۀ نسبی کم اشاره کرد.
فرآیندهای متداول ریخته گری در ساخت قطعات خودرو شامل کوره ریخته گری (در قالب) ماسه ای یا Sand Casting، ریخته گری ثقلی (در قالب فلزی) یا Gravity Die Casting، ریخته گری تحت فشار بالا در قالب فلزی یا High Pressure Die Casting و ریخته گری تحت فشار پایین در قالب فلزی یا Low Pressure Die Casting می باشند.
پروسۀ ماشینکاری نیز یکی دیگر از روش های متعدد ساخت قطعات بوده به گونه ای که یک قطعه ماده ( یا فلز) خام به شکل و اندازۀ نهایی موردنظر توسط فرآیند مربوط بریده می شود. در این متد هم روش های متنوعی در ماشینکاری قطعات خودرو مورد استفاده قرار می گیرند که می توان از فرآیند فرزکاری (Milling)، تراشکاری (Lathing)، منگنه زنی (Punching)، برشکاری (Cutting)، اره کاری، خمکاری و … نام برد. البته ماشین ابزارهایی نیز وجود دارند که در ساخت قطعات خودروهای خاص و مسابقه ای استفاده می شوند. از جمله ماشینکاری با اشعۀ الکترونی و یونی، برشکاری لیزری، قوس پلاسما و …
کوره ریخته گری چگونه انجام میشود؟
با وجود روشهای مختلف برای اجرای کوره ریخته گری، این فرآیند، معمولا طی چندین مرحله کلی شامل ساخت الگو، ساخت ماهیچه، ساخت قالب، ذوب کردن فلز، ریختن ماده مذاب به درون قالب، انجماد، باز کردن قالب و پرداخت قطعه انجام میگیرد.
فعالیتهای موجود در هر یک از کوره ریخته گری این مراحل عبارت هستند از:
مدلسازی: طراحی قالب های صنعتی مورد استفاده در فرآیند کوره ریخته گری توسط نرم افزارهای تخصصی و ساخت مدل فیزیکی قطعه نهایی
ساخت ماهیچه: طراحی و ساخت ماهیچههای مورد نیاز برای ایجاد سطوح داخلی قطعه
قالب سازی: ساخت قالب کوره ریختهگری با توجه به مستندات طراحی و با استفاده از موادی نظیر ماسه، موم، فولاد و غیره
ذوب و ریختن: اعمال دمای بالا به فلزات برای تبدیل به حالت مایع و ریختن مواد مذاب به درون قالب توسط بوته یا دیگر تجهیزات موجود
انجماد: کاهش دمای قالب و مواد مذاب درون آن پس از اتمام فرآیند ریختن
باز کردن قالب: جدا کردن بخشهای مختلف قالب و خارج کردن قطعه قالب ریخته گری شده
پرداخت: اجرای برشکاری، سنگزنی، سندبلاست و غیره به منظور جدا کردن بخشهای اضافی قطعه، ایجاد بافت مناسب و یا آمادهسازی سطح آن برای پوششدهی
پودر کوره ریخته گری
گروه دانش بنیان پاترون اولین تولیدکننده پودر قالب ریخته گری در ایران، با نام تجاری کستینگ پات است. این شرکت از سال 1393 دست به تولید این محصول زد و در سال 1396 نیز موفق شد برای اولین بار در کشور گرید گرانوله آن را تولید نماید.
پودر قالب ریختهگری مداوم به عنوان یک روانکار به سطح مذاب موجود در قالب اضافه می شود تا موجب تسهیل عبور شمش یا اسلب یا بلوم از درون آن شود. با اضافه کردن پودر قالب به سطح مذاب، این پودر با نرخ معینی ذوب شده و یک سربارهی شیشه ای مذاب تشکیل میدهد. این سرباره همانند یک فیلم نازک بین تیوپ مسی و پوسته فولادی منجمد شده قرار گرفته و به عنوان یک روانساز بین این دو عمل میکند. همچنین پودر مذکور عایق حرارتی بوده و موجب جذب ناخالصیهای ذوب نیز میگردد. یکی دیگر از وظایف پودر ریخته گری جلوگیری از اکسیداسیون سطح ذوب در مجاورت با هواست. جذب ناخالصی های ذوب منجر یه کاهش حفرات ریز زیرسطحی نیز میشود.
بر اساس شرایط مختلف ریخته گری، گروه پاترون ده ها گرید از این محصول را تولید میکند. در واقع گروه پاترون یکی از معدود شرکتهای تولیدکننده پودر ریخته گری در منطقه است که دانش فنی تولید انواع آن را دارد. این محصول پاترون با گریدهای مختلف آن، در بسیاری از محصولات حساس، از جمله فولادهای آلیاژی یا تولید ریل در ذوب آهن اصفهان مورد استفاده قرار گرفته یا جایگزین محصولات خارجی گردیده است. همچنین صادرات این محصول به کشورهای همسایه در طی سالهای گذشته باعث رضایت مشتریان خارجی نیز گردیده است.
گروه پاترون برای مشتریانی که نیازمند نوع گرانوله پودر ریخته گری هستند نیز این محصول را برای اولین بار در کشور تولید کرده و قادر است برای هر شرایط ریخته گری، نوع گرانوله آن را نیز طراحی و تولید نماید.
نوع دیگری از کستینگ پات، پودر قالب اینگات است که با نام تجاری اینگوپات تولید میشود. این نوع پودر، در بسته بندی مخصوص، برای قالب های عمودی اینگات طراحی و تولید میشود که مشتریان خاصی از جمله فولاد آلیاژی ایران دارد. توان بالای طراحی و کیفیت محصول گروه پاترون باعث شده این محصول نیز جایگزین محصولات خارجی گردد.
مقایسه کستینگ پات گروه پاترون با دیگر محصولات در مجموع نشان میدهد که کستینگ پات ضریب مصرف کمتر، کیفیت سطحی (مثل حفرات سطحی، ترک عرضی و طولی، پوسته و یا اثر اوسیلیشن) و داخلی (مثل حفرات زیر سطحی) بالاتر شمش، بلوم، اینگات یا اسلب فولادی داشته و به عمر بیشتر تیوب مسی کمک میکند. مقایسه های بسیاری از این دست انجام شده و نامه های رضایت مندی مشتریان تایید کننده این موضوع است.
به طور معمول گروه پاترون برای مشتریان جدید و یا برای درخواست های جدید مشتریان قبلی، با ارسال فرم، اطلاعات لازم برای طراحی پودر ریخته گری را به دست آورده، با ارسال نمونه، نظارت بر مصرف و آموزش، نسبت به اخذ تاییدیه و تولید انبوه آن گرید خاص اقدام میکند.
مواد مورد استفاده در کوره ریخته گری چه هستند؟
چدن خاکستری، پرکاربردترین ماده مورد استفاده در فرآیند کوره ریخته گری است. از دیگر فلزات متداول در این فرآیند میتوان به چدن نشکن، آلومینیوم، فولاد، مس و روی اشاره کرد. البته امکان استفاده از مواد غیر فلزی مانند بتن، شیشه، پلاستیک و رزین نیز برای ساخت قطعات کوره ریختهگری وجود دارد. انتخاب ماده مناسب برای ساخت قطعات، به پارامترهایی نظیر حجم تولید، صرفه اقتصادی، دمای ذوب، سرعت خنککاری، مقاومت در برابر فرسودگی، وزن و قابلیت جذب ارتعاش بستگی دارد. نوع ماده مورد استفاده، یکی از معیارهای تقسیمبندی انواع روش های ریخته گری و کاربردهای آنها است.
کاربرد کوره ریخته گری چیست؟
کوره ریخته گری، تقریبا در تمام صنایع کاربرد دارد. حدود 90 درصد از محصولات تولید شده در صنایع مختلف و ماشینآلات صنعتی، به نحوی با فرآیندهای کوره ریخته گری در ارتباط هستند. با این وجود، بیش از 50 درصد از قطعات ریخته گری شده در صنایع ساخت ماشینآلات سنگین و تجهیزات حمل و نقل مورد استفاده قرار میگیرند.
اصطلاحات کوره ریخته گری، یکی از متداولترین روشهای ساخت و تولید است که طی چندین مرحله و با استفاده از ابزارهای متنوع اجرا میشود. یادگیری اصطلاحات رایج کوره ریخته گری، امکان درک بهتر مکانیزم اجرای این فرآیند را فراهم میکند. برخی از این اصطلاحات عبارت هستند از:
اصطلاحات مربوط به ابزارهای کوره ریختهگری
قالب
حفره
سیستم راهگاهی
قطعه
ماسه ریخته گری
ماسه رویه
ماسه رزینی
فلاسک
کوپ و درگ
چیک
مدل
ماهیچه
چپلت
چیل
بوته
پاتیل
اصطلاحات مربوط به سیستم راهگاهی درون قالب کوره ریخته گری
حوضچه
بارریز
اسپرو
چشمه
رانر
گیت
رایزر
غلاف
هواکش
در ادامه به معرفی هر یک از اصطلاحات بالا میپردازیم
قالب کوره ریخته گری«قالب» (Mold یا Mould)
ابزاری است که به منظور شکلدهی به فلز مذاب مورد استفاده قرار میگیرد. قالب کوره ریختهگری تحت فشار با اصطلاح «دای» (Die) شناخته میشود. طراحی قالب های صنعتی مورد استفاده از فعالیتهای بسیار مهم در فرآیند ریختهگری به شمار میرود؛ چراکه تمامی بخشهای موجود در قالب، بر روی کیفیت قطعه ریخته گری شده تاثیر میگذارند.
حفره قالب
«حفره» (Cavity)، فضای خالی درون قالب و مقصد نهایی مواد مذاب است. مواد مذاب با پر کردن حفره قالب، ساختار کلی قطعه مورد نظر را تشکیل میدهند.
سیستم راهگاهی قالب
«سیستم راهگاهی» (Gating system)، مجموعهای از مجراهای درون قالب است که امکان هدایت مواد مذاب از بیرون قالب به درون حفره را فراهم میکند. حوضچه، اسپرو، چشمه، راهبار، تغذیه، راهبار، راهباره و دریچه، از بخشهای اصلی سیستم راهگاهی به شمار میروند.
قطعه ریخته گری شده
قطعه ریخته گری شده، جسمی است که پس از فرآیند انجماد از درون حفره قالب خارج میشود. به قطعه ریخته گری شده، اصطلاحا «کستینگ» (Casting) میگویند.
ماسه ریخته گری
ریخته گری ماسه ای به عنوان متداولترین روش اجرای ریختهگری شناخته میشود. ماده اصلی در ساخت قالبهای این فرآیند، ماسه است. فراوانی و هزینه پایین ماسه سیلیسی، این ماده را به گزینه اول ساخت قالبهای ماسهای تبدیل میکند. البته انبساط حرارتی بالای ماسه سیلیسی، احتمال رخ دادن عیوب ریخته گری را افزایش میدهد. ماسه تر یا ماسه سبز، سیلیکات سدیم یا شیشه مایع و ماسه رزینی از رایجترین مواد مورد استفاده برای ساخت قالبهای ریختهگری هستند.
ماسه رزینی
ماسه رزینی، مادهای است که معمولا از ترکیب ماسه سیلیسی ریزدانه با رزین فنولی ترموست تشکیل میشود. مخلوط کردن این مواد با یکدیگر، امکان ساخت قالبهای سخت با استحکام بالا را فراهم میکند.
ماسه رویه
«ماسه رویه» (Facing Sand)، ماسهای است که برای ساخت بخشهای قالب کوره ریخته گری در مجاورت مدل استفاده میشود. ماسه رویه در ارتباط مستقیم با مواد مذاب قرار میگیرد. از اینرو، این ماسه از مقاومت بسیار بالایی در برابر تنشهای حرارتی اعمال شده از طرف مواد مذاب بهره میبرد.
درجه یا فلاسک
دُرجه یا «فلاسک» (Flask)، ابزاری است که به منظور نگهداری قالب کوره ریخته گری مورد استفاده قرار میگیرد. این وسیله، فقط دارای دیوارههای جانبی است و هیچ بخش بالایی یا پایینی ندارد. مقطع فلاسک، معمولا به شکل مقاطع سادهای نظیر مربع، مستطیل و دایره است.
چیک
در ریختهگریهای پیچیده، فلاسک، از چندین تکه (بیش از دو تکه) تشکیل میشود. به بخشهای میانی فلاسک در این حالت، «چیک» (Cheek) میگویند.
مدل یا الگو
مدل یا «الگو» (Pattern)، جسمی کاملا مشابه با قطعه نهایی ریخته گری است. این جسم به منظور ایجاد حفره قالب (فضای جریان یافتن مواد مذاب) مورد استفاده قرار میگیرد. از مواد قابل استفاده برای ساخت مدل ریخته گری میتوان به چوب، فلز و پلاستیک اشاره کرد.
مغزه یا ماهیچه
ماهیچه یا «مغزه» (Core)، قطعهای مجزا در قالب کوره ریخته گری است که به منظور ایجاد بازکننده و فضاهای توخالی در قطعه مورد استفاده قرار میگیرد. در صورت پیچیدگی ساختار داخلی قطعه و عدم امکان دستیابی به شکل مورد نظر توسط مدل، از ماهیچه درون حفره قالب استفاده میشود. به این ترتیب، مواد مذاب، محل قرارگیری ماهیچهها را پر نمیکنند. ماهیچهها از ابزارهای پرکاربرد در فرآیندهای ریختهگری به شمار میروند.
چپلت
«چپلت» (Chaplet)، قطعه کوچک فلزی است که در کوره ریخته گری ظبه منظور نگهداری ماهیچه در حین فرآیند ریخته گری مورد استفاده قرار میگیرد. چپلتها، از جابجایی ماهیچه بر اثر نیروهای اعمال شده از طرف جریان مواد مذاب جلوگیری میکنند.
چیل
«چیل» (Chill)، قطعهای است که به منظور بهبود فرآیند انجماد (افزایش نرخ خنک شدن)، درون حفره قالب یا اطراف آن جانمایی میشود. در ریختهگریهای پیچیده، عدم تقارن شکل و ضخامت قطعات، از انجماد خطی و یکنواخت بخشهای مختلف جلوگیری میکند. چیلها، با تنظیم انتقال حرارتی در نقاط بحرانی، باعث تعدیل فرآیند انجماد میشوند. جنس این قطعات از مواد دارای هدایت الکتریکی بسیار بالا است.
بوته
«بوته» (Crucible)، ظرفی است که به منظور نگهداری فلزات در حین فرآیند ذوب مورد استفاده قرار میگیرد. بوته ریخته گری معمولا از جنس مواد سرامیکی یا فلزی با نقطه ذوب بسیار بالا ساخته میشود. این وسیله درون کوره قرار میگیرد و حرارت کوره را به فلز درون خود انتقال میدهد. پس از ذوب شدن فلز، بوته برای شروع فرآیند ریختهگری به محل قرارگیری قالب انتقال داده میشود
پاتیل
«پاتیل» (Ladle)، وسیلهای است که منظور انتقال و ریختن ماده مذاب در فرآیند ریخته گری مورد استفاده قرار میگیرد. پاتیلها اغلب در کارخانههای ذوب کاربرد دارند. این وسایل در ابعاد کوچک (با ظرفیت حدود 20 کیلوگرم) و بزرگ (با ظرفیت حدود 330 تن) ساخته میشوند. برخلاف بوته، پاتیلهای معمولی درون کوره قرار نمیگیرند. برخی از کورههای پایتلی، از قابلیت اعمال حرارت به فلز و ذوب آن بهره میبرند.
حوضچه بارریز
«حوضچه بارریز» (Pouring Basin)، یک حفره کوچک قیفی شکل در بخش بالایی قالب است که در کوره ریخته گری به منظور ریختن مواد مذاب به درون حفره داخلی استفاده میشود. حوضچه بارریز، نرخ جریان مواد مذاب را تنظیم میکند و اغتشاشات مواد در ورودی راهگاه را کاهش میدهد. تصویر زیر، بیانگر بخشهای مختلف قالب ریختهگری ماسهای و سیستم راهگاهی درون آن است. اصطلاحات مورد استفاده در اغلب روشهای ریختهگری، به یکدیگر شباهت دارند.
اسپرو یا راهگاه بارریز
راهگاه بارریز یا «اسپرو» (Sprue)، مجرای هدایت مواد مذاب از حوضچه بارریز به حفره قالب است. این مجرا، معمولا به شکل مخروطی طراحی و ساخته میشود. در بسیاری از موارد، کنترل جریان مواد مذاب توسط راهگاه بارریز انجام میگیرد.
چشمه راهگاه
در انتهای راهگاه بارریز و در محل اتصال آن با راهبار، فضایی وجود دارد که با تجمع مواد مذاب، از سقوط آزاد آنها جلوگیری میکند. به این فضا، چشمه راهگاه میگویند. چشمه راهگاه، اغتشاشات جریان و گیر کردن هوا درون مواد مذاب را کاهش میدهد. مقطع این چشمه معمولا به شکل دایره، قطر آن حدود دو برابر قطر انتهای راهگاه و عمق آن حدود دو برابر عمق راهبار است.
رانر یا راهبار
راهبار یا «رانر» (Runner)، مجرایی است که مواد مذاب را از راهگاه به دریچه یا تغذیه های اطراف حفره قالب هدایت میکند. رانرها با کاهش سرعت مواد مذاب، باعث جریان یکنواخت آنها به بخشهای مختلف حفره میشوند. این مجراها، معمولا در بخش پایینی قالب قرار دارند.
دریچه یا راهباره
راهباره یا دریچه «Gate یا Ingate»، مجرایی است که مواد مذاب را از راهبار به حفره اصلی قالب هدایت میکند. طراحی راهباره، باعث تغذیه یکنواخت حفره با نرخ ثابت و مطابق با نرخ انجماد میشود. در اغلب موارد، مقداری از مواد مذاب درون دریچه یا حتی دیگر مجراهای سیستم راهگاهی باقی میمانند. این مواد به همراه مواد درون حفره، طی فرآیند انجماد، سخت میشوند. از اینرو، پس از باز کردن قالب و خارج کردن قطعه، نیاز به عملیات ماشینکاری برای تهیه قطعه یا قطعات نهایی خواهد بود.
رایزر یا تغذیه
منبع تغذیه یا «رایزر» (Riser)، فضاهایی درون سیستم راهگاهی قالب هستند که در هنگام توقف ریختن مواد مذاب، به عنوان مخازن ذخیره و تامین مواد مورد استفاده قرار میگیرند. با توقف فرآیند ریختن، مواد مذاب درون حفرهها، بر اثر فرآیند انجماد، شروع به جمع شدن میکنند. کاهش حجم ناشی از جمعشدگی، باعث کاهش ابعاد و تغییر شکل قطعه ریختهگری شده نسبت به قطعه طراحی شده میشود. رایزرها، با تامین مواد مذاب اضافی، تاثیر جمعشدگی بر مشخصات ابعادی قطعه را کاهش میدهند. بر اساس دسترسی یا عدم دسترسی مجرا به بیرون قالب، رایزرها به انواع بالاسری (دسترسی از بالای قالب)، کناری (دسترسی از کنارههای قالب) و کور (بدون دسترسی) تقسیم میشوند.
غلاف رایزر
«غلاف رایزر» (Riser Sleeve)، قطعهای استوانهای شکل است که در کوره ریخته گری به منظور کاهش افت حرارتی رایزر توسط ایجاد عایق حرارتی و یا تولید حرارت برای جلوگیری از افت دما مورد استفاده قرار میگیرد. این قطعه، با کاهش میزان جمعشدگی، باعث پیوستگی فرآیند ریختهگری و افزایش کیفیت قطعه نهایی میشود.
هواکش
«هواکش» (Vent)، مجرای کوچکی است که امکان خروج هوا و گازهای ایجاد شده در قالب را فراهم میکند. طراحی مناسب هواکشها، از اهمیت بالایی برای جلوگیری از عیوب ریختهگری مرتبط با حضور گازها برخوردار است. هر چه سطح هواکشها از مقاومت کمتری در برابر جریان هوا برخوردار باشد، خروج گازها با سهولت بیشتری انجام میگیرد.
مزایای انواع کوره ریخته گری:
امکان ساخت قطعات پیچیده با هزینه نسبتا کم
عدم تاثیر ابعاد قطعه مورد نظر بر روی فرآیند
خواص مکانیکی بسیار خوب قطعه نهایی
امکان ساخت قطعات با جزئیات ریز و دقیق
عدم وجود محدودیت در مواد قابل استفاده
ساختار داخلی یکنواخت و همسانگرد قطعه
صرفه اقتصادی نسبت به دیگر روشهای ساخت
امکان ساخت قطعات کامپوزیتی (متشکل از چندین ماده)
معایب انواع کوره ریخته گری
به مشکلات ایجاد شده در ساختار قطعه طی فرآیند ریختهگری، عیوب ریخته گری میگویند. هر یک از روش های ریخته گری، مستعد رخ دادن عیب و نقصهای مختص به خود هستند. برخی از این عیب و نقصها، کیفیت و عملکرد قطعه را تحت تاثیر قرار میدهند. به همین دلیل، این عیوب، معمولا طی فرآیندهای کنترل کیفیت شناسایی میشوند.
از رایجترین نواقص احتمالی در قطعات ساخته شده به روش کوره ریختهگری میتوان به موارد زیر اشاره کرد:
عدم انطباق: عدم جانمایی مناسب نیمههای قالب و ماهیچه
تورم: افزایش ابعاد حفره قالب به دلیل فشار زیاد مواد فشار
جوشیدن (سوسه و مک): محبوس شدن گاز در سطح قطعه به دلیل فرآیند انجماد
ماسه ریزی: وجود ترک بر روی سطح بالایی ماسه و اضافه شدن ذرات ماسه به درون فلز مذاب
نفوذ فلز: سطوح ناهموار و زبر قطعه به دلیل دانهبندی بزرگ ماسه و نفوذ مواد مذاب به درون قالب
حفرههای کوچک: حفرههای بسیار ریز (حدود 2 میلیمتر) بر روی سطح قطعه به دلیل آزاد شدن گاز هیدروژن از مواد مذاب
حفرههای انقباضی: ایجاد حفرههای داخلی ناشی از کاهش حجم قطعه در حین انجماد
اتصال سرد: به جا ماندن اثر خط برخورد مواد مذاب در قالبهای دارای دو مجرای ورودینیامد: انجماد مواد مذاب قبل از پر کردن کامل تمام حفرهآخال سربارهای: وجود ذرات سرباره درون مواد مذاب
ترک گرم: شکست کششی ناشی از تنشهای پسماند در مواد مذاب
سخت ریزه: انجماد سریعتر برخی از نقاط نسبت به مواد اطراف
ماهیچه ماسهای: حفرههای داخلی یا خارجی ناشی از ورود ذرات سست ماسه به درون حفره قالب یا ریختن سریع مواد مذاب به درون قالب
لکه: ناهمواری سطح قطعه به دلیل وجود ذرات اضافی بر روی سطح داخلی قالب
حفرههای شبکهای: ایجاد چندین حفره کوچک و نزدیک به هم در سطح خارجی قطعه
تابیدگی: تغییر شکل قطعه در حین انجماد یا پس از انجماد به دلیل یکنواخت نبودن نرخ کاهش دمای
موادپلیسه: ایجاد لایه نازک
كوره هایي كه در کوره ريخته گري براي ذوب مجدد فلزات و آلياژها استفاده مي شوند به ترتيب مي توانيم به شرح زير نام ببريم :
1) كوره هاي بوته اي Crucible Furnaces:
یکی از متداول ترین و ارزان ترین نوع کوره های ریخته گری کوره های بوتهای یا زمینی است. این کورهها به علت کاربری آسان و هزینه های پایین پر کاربردترین نوع کوره در صنعت ریخته گری محسوب میشوند.
مزایای کورهریخته گری زمینی به شرح زیر است:
- آسان بودن کاربری
- هزینه ساخت کم
- فراوانی سوخت مصرفی
- کم بودن میزان اتلاف عناصر
- قابلیت ذوب انواع فلزات
معایب کوره ریخته گری زمینی به شرح زیر است:
- پایین بودن راندمان (10 -15) درصد
- ظرفیت کم
2) كوره هاي تشعشعي Radiation or Reverberatory Furnaces:
در کورههای تشعشعی برای ذوب مواد سوخت مستقیماً با مواد تماس ندارد بلکه بین محصول احتراق و مواد تماس مستقیم برقرار میشود. یعنی با شعله و گازهای احتراق داغی که از دیگری بر روی آن منفجر میشود آن را گرم میکند.
مزایای کورههای تشعشعی به شرح زیر است:
- کنترل دمای کافی
- هزینه های عملیاتی و نگهداری پایین
- سرعت پردازش در حجم بالا
- کنترل ترکیب شیمیایی کافی
معایب کورههای تشعشعی به شرح زیر است:
- پایین بودن سطح کنترل فضای کوره
- اشغال کردن فضای کف زیاد
- بالا بودن هزینههای اولیه
- وجود تلورانس( 50 +/- درجه فارنهایت) در تغییرات دمای فلز
- فضای محدود کوره
- جذب گاز هیدروژن بیشتر در ذوب آلومینیوم
- برآورد نشدن کنترل دقیق در ترکیبات شیمیایی
3) كوره هاي ریخته گری ايستاده (كوپل) Vatical Shaft (Cuple) Furnaces:
کورههای کوپل ساختمان بسیار سادهای داشته و قدمت آنها به 403-221 قبل از میلاد باز میگردد. کورههای ذوب کوپل اولین بار در چین مورد استفاده قرار گرفته اند. این نوع کورهها بیشتر برای ذوب چدن قراضه به کار میروند و بعد از کورههای زمینی مرغوبترین چدن را تولید میکنند.
مزایای کورههای ریخته گری کوپل به شرح زیر است:
- هزینه اولیه پایین
- نرخ ذوب بالا
- هزینه عملیاتی بسیار پایین
- آسان بودن کاربری
- بازدهی از 30% تا 50%
- کنترل ترکیب شیمیایی کافی
معایب کورههای ریخته گری کوپل به شرح زیر است:
- دشوار بودن نگهداری و کنترل دما
- امکانپذیر نبودن کنترل دقیق ترکیب شیمیایی
- از بین رفتن عناصرSi و Mn
4) کوره های ذوب روباز :
در این نوع از کوره های ذوب و ریخته گری ، این یک فرآیند ساخت فولاد جایگزین است که در آن از گاز طبیعی، روغن، روغنهای سنگین اتمی، قطران، یا زغال سنگ پودر شده به عنوان سوخت استفاده میشود. هوا و سوخت هر دو قبل از احتراق تا حدود 800 درجه سانتیگراد گرم میشوند. دمای شعله حدود 2000 درجه سانتیگراد بدست میآید و این برای ذوب شدن شارژ کافی است. در ابتدا تا 10 تن شارژ میشود، اما ظرفیت کوره به تدریج به 100، 300 و در نهایت به 600 تن افزایش مییابد.
عملکرد این کوره بدینصورت است که در صورت ذوب شدن مجدد ضایعات فولادی، کوره با ضایعات سبک مانند ورق فلز، وسایل نقلیه خرد شده یا ضایعات فلز شارژ میشود. هنگامی که قراضههای سبک ذوب میشوند، قراضههای سنگین مانند قراضههای ساختمانی و فرز فولادی اضافه میشود.
پس از ذوب شدن تمام فولاد، مواد تشکیل دهنده سرباره، مانند سنگ آهک، اضافه میشوند. اکسیژن موجود در اکسید آهن و سایر ناخالصیها با سوزاندن کربن و تشکیل فولاد، آهن خام را دفع میکند. برای افزایش میزان اکسیژن، میتوان سنگ آهن اضافه کرد.
تهیه یک کوره معمولاً 8 ساعت تا 8 ساعت و 30 دقیقه طول میکشد. میتوان برای ایجاد ترکیب مورد نظر، بر روی فولاد افزودنیهایی اضافه کرد. پس از مدتی، جهت جریان هوا و سوخت معکوس میشود. محفظههایی که از چرخه قبلی گرم میشوند، به نوبه خود سوخت و هوای ورودی را گرم میکنند.
اکثر کورههای کوره باز از نظر شیمیایی اساسی هستند. کوره های اساسی میتوانند فسفر، گوگرد، سیلیسیم، کربن و منگنز را از فلز شارژ خارج کنند. کوره از طریق یک سوراخ شیر واقع در کنار کوره قرار میگیرد و اجازه میدهد تا فولاد مذاب خارج شود. پس از ضربه زدن به تمام فولادها، سرباره از بین میرود.
درادامه ممکن است در شمش ریخته شود یا در ریخته گری مداوم برای دستگاه نورد استفاده شود.
مزایای کوره ریخته گری ذوب روباز :
1-مزیت بزرگ کوره باز انعطاف پذیری آن است: بار میتواند تمام ضایعات سرد یا هر ترکیبی از آهن و قراضه باشد.
2-کوره قادر به پردازش آهن تقریباً با هر ترکیب شیمیایی هستند.
3-این فرایند برای رسیدگی به هر مقدار ضایعات فولاد کم هزینه مناسب است.
4-کورههای کوره باز میتوانند با هر نوع سوخت کار کنند.
5-کیفیت کوره در بین فرآیندهای ساخت فولاد تجاری Bessemer، Thomas و روشهای مبدل اکسیژن بالاترین کیفیت را دارد.
6-کنترل دما کافی.
7-کنترل ترکیب شیمیایی کافی.
معایب کوره ریخته گری ذوب روباز :
1-هزینه اولیه بالا
2-نیاز به فضای کف بزرگ.
3- فرایند از نوع دسته ای است
4-بهره وری پایین در مقایسه با فرآیند مبدل اکسیژن.
5-ضرورت تهیه شار و بازسازی کننده ها (مانند عناصر آلیاژی) باعث افزایش هزینه های ساخت و راه اندازی کوره های گرم کن باز میشود.
6-کنترل دقیق دمای مذاب قابل انجام نیست.
7-کنترل دقیق ترکیب شیمیایی برآورده نمیشود.
8-کنترل محدود جو کوره
۵) کوره های قوس الکتریکی
در این نوع، شعله با مواد مذاب در ارتباط است. با دادن جریان الکتریکی بین دوتا الکترود یک قوس الکتریکی ایجاد می شود که قدرت زیادی دارد. الکترودها به داخل کوره می روند و می توانند این جریان را به مواد شارژ شده داخل کوره انتقال دهد. دمای ایجاد شده در آن محدود تقریباً 3000 درجه می باشد. نکته دیگر درباره کوره قوس الکتریکی استفاده از آهن قراضه برای مواد اولیه است واین امکان وجود دارد که از بدترین آهن قراضه بهترین فولاد را تهیه کنند.آسو صنعت در صنایع تولید و ساخت انواع کوره ذوب و همچنین فروش و نصب بگ فیلترهای سنتی و صنعتی پیشتاز بود و با جلب رضایت مشتریان توانسته جایگاه خوبی پیدا کند.
انواع کوره ریخته گری:
قالبهای یکبار مصرف: ریخته گری در قالبهای موقتی و بدون امکان استفاده مجدد
کوره ریختهگری ماسه ای : یکی از روش های متداول برای ریخته گری، استفاده از ماسه برای قالب گیری می باشد. ماسه هایی که برای این روش ریخته گری استفاده می شوند به صورت طبیعی و یا ترکیبی می باشند. نمونه ی ترکیبی در واقع ماسه دریاچه می باشد. البته توجه داشته باشید که اگر قالب بسیار بزرگ باشد می توان از ماسه سبز استفاده کرد. ماسه سبز از آب، ماسه و خاک رس تشکیل می شود.
برای تعیین میزان نسبت ماسه به فلز ، باید به روش قالب گیری، اندازه ی قطعات مورد نظر، نوع فلز و … توجه داشت. اما به طور معمول می توان نسبت ماسه به فلز را حدود 4 الی 5 به یک در نظر گرفت. مثلا برای تهیه ی یک تن ریخته گری، باید حدود 4 تا 5 تن ماسه استفاده کرد.
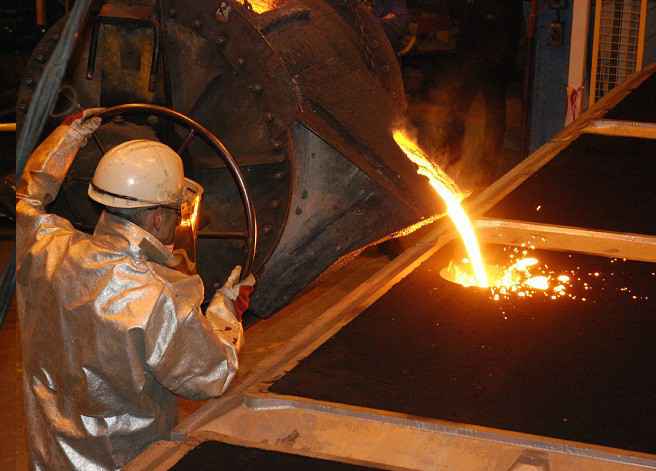
مزایای کوره ریخته گری ماسهای:
هزینههای تولید نسبتاً ارزان، به خصوص در نمونههای کم حجم.
توانایی ساخت قطعات بزرگ.
ظرفیت ریخته گری مواد آهنی و همچنین مواد غیر آهنی.
هزینه کم ابزار برای فرآیندهای پس از ریخته گری.
معایب کوره ریخته گری ماسهای:
دقت ابعادی پایینتر ریختهگری ماسهای نسبت به سایر فرایندهای ریخته گری،وزن ریختهشده معمولاً از وزن محاسبه شده بیشتر است.
سطح نهایی قطعه ریختهگری شده آهنی معمولاً از RMS125 فراتر میرود.
علاوه بر این، این فرایند تمایل به تولید محصولاتی با سطح نسبتاً خشن دارد.
کوره ریختهگری گچی : در این روش ، از قالب های گچی استفاده می شود به همین سبب نام آن را ریخته گری گچی نامیده اند. قالب های مورد استفاده در این روش از گچ فرنگی و افزودنی های دیگر ساخته می شوند. قطعاتی که به دقت بالا نیاز دارند، مانند قطعات مکانیکی باید با این روش ساخته شوند.
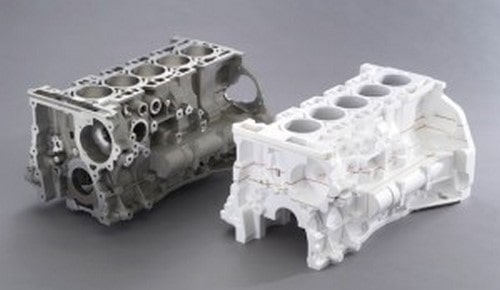
کوره ریختهگری پوسته ای : قالب پوسته ای قالبی است که از سخت شدن مخلوط ماسه بر روی یک مدل فلزی داغ شکل می گیرد. برای ساخت قالب پوسته ای، مدل فلزی (معمولاً از جنس آلومینیوم یا چدن خاکستری) را معمولاً در حدود ۲۶۰-۱۵۰ درجه سانتیگراد گرم می کنند.
سپس مخلوط ماسه (معمولاً ماسه سیلیسی یا زیرکنی) با یک چسب رزینی گرماسخت را در تماس با سطح مدل داغ قرار می دهند. در اثر گرمای مدل، چسب مخلوط ماسه فعال شده و باعث چسبیدن ذرات ریز ماسه به هم و به سطح مدل فلزی می شود. پس از سخت شدن قالب، آن را از سطح مدل جدا می کنند.
به این ترتیب، یک قالب ماسه ای به شکل پوسته ای با دیواره های تقریباً نازک ساخته می شود که شکل مدل در داخل آن ایجاد شده است. پس از جاگذاری ماهیچه و مونتاژ دو نیمه ی قالب پوسته ای بر روی هم، قالب آماده ی ذوب ریزی است. به فرایند ریخته گری با این قالب ها، ریخته گری در قالب های پوسته ای (Shell Mold Casting) می گویند.
کوره ریختهگری دقیق : یکی دیگر از روش های با ارزش در این صنعت ، روش ریخته گری دقیق نام دارد. این روش با نام های ریخته گری ظریف و ریخته گری با مدل های مومی نیز شناخته می شود.
در این روش از مواد دیر گداز و قالب های سرامیکی استفاده می شود تا بتوان به وسیله ی آن ها قطعاتی با کیفیت بالا تهیه کرد. قطعات و مدل هایی که با این روش دقیق و ظریف ساخته می شود، بسیار صاف و یک دست می باشند. به همین دلیل افراد اگر بخواهند قطعات پیچیده را بسازند باید از این روش استفاده کنند.
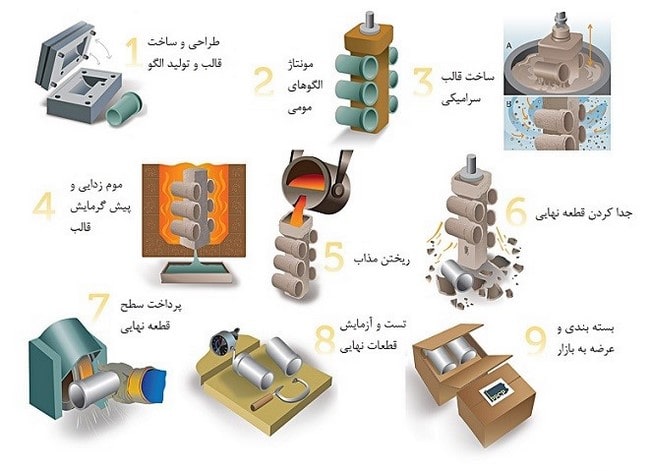
کوره ریختهگری الگوی تبخیری :یکی از انواع کوره ریخته گری است که از الگوی ساخته شده از ماده ای که هنگام ریخته شدن فلز مذاب در حفره قالب تبخیر میشود و متداول تریت ماده الگوی تبخیری مورد استفاده فوم پلی استایرن است
قالبهای دائمی: ریخته گری در قالبهای چندبار مصرف و بدون نیاز به اعمال تغییر بر روی قالب پس از هر چرخه تولید
کوره ریختهگری ثقلی : یکی از روش های ریخته گری صنعتی، ریخته گری ثقلی نامیده می شود. در این روش از چند قالب فلزی استفاده می شود تا بتوان قطعه ای خاص را تولید کرد. زمانی که مواد درون قالب ها ریخته می شوند، قالب بر اساس وزن و نیروی ثقل پر می شود به همین سبب به این روش ثقلی گفته می شود.
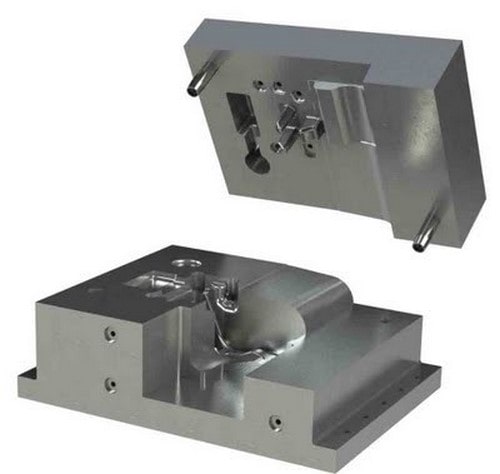
کوره ریختهگری تحت فشار (دایکاست): یکی از سریع ترین و بهترین روش های ریخته گری، روش تحت فشار می باشد. در این روش مواد مذاب با فشار زیاد به درون قالب های مورد نظر ریخته می شوند. این فشار زیاد باعث می شود که گاز های متصاعد درون قالب باقی نمانند و طرح نهایی بدون حفره های درون و مک آماده شود. از مهم ترین مزایای این روش می توان به محکم بودن قطعات ساخته شده و بدون حفره و یک دست بودن آن ها اشاره کرد. به دلیل مزایا و ویژگی های خاص این روش، افراد زیادی به آن روی آورده اند.
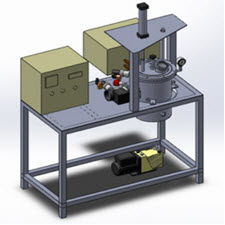
کوره ریختهگری نیمه جامد: به ریخته گری آلیاژی گفته میشود که دمای انجماد آنها در محدوده ی بین خطوط لیکوییدوس و سالیدوس باشد ریخته گری این نوع مواد که حدود ۳۰سال پیش مورد توجه قرار گرفته و به عنوان یک تعریف ساده ماده نیمه جامد مخلوطی از فاز جامد و مایع بوده و فرایند نیمه جامد تشکیل یک مخلوط از ذرات کروی فاز جامد معلق در فاز مایع است.
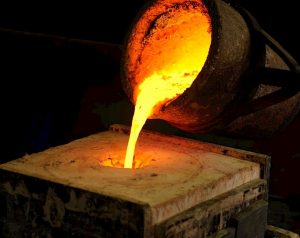
کوره ریختهگری گریز از مرکز :فلز مذاب وارد قالب می شود که به طور مداوم در طول کل فرآیند ریخته گری چرخانده می شود. قالب خود بسته به نیاز طراحی می تواند به صورت افقی یا عمودی چرخانده شود.
به طور معمول از دستگاهی با طراحی افقی برای تولید استوانه ای نازک در حالی که دستگاه های نصب شده به صورت عمودی برای تولید حلقه ها یا محصولات مشابه استفاده می شود.
اما گاهی اوقات استوانه های کوچکتر نیز با استفاده از یک فرآیند گریز از مرکز عمودی تشکیل می شوند در حالی که از آرایش افقی برای ساختار لوله ای طولانی استفاده می شود.
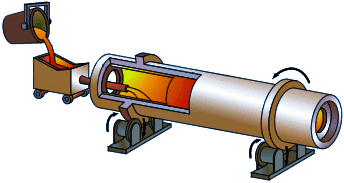
کوره ریختهگری پیوسته : از روش ریخته گری مداوم، میتوان به عنوان پرکاربردترین نوع ریخته گری مقاطع میانی یاد کرد. این روش ریخته گری که سرعت بالایی در ساخت قطعات دارد، معمولا به صورت عمودی مورد استفاده قرار میگیرد. مذاب فولاد پس از آماده سازی از کوره قوس به پاتیل منتقل میشود. در بخش ریخته گری مذاب در یک تاندیش تخلیه میشود. خروجی تاندیش در چند خط ریخته گری تقسیم میشود.
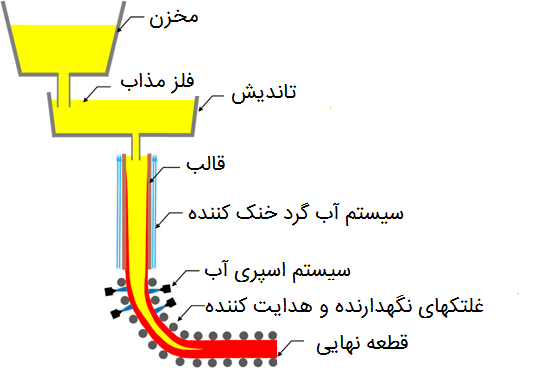
ریخته گری کوبشی :کوره ریخته گری کوبشی یکی دیگر از روش های کوره ریخته گری محسوب میشود که در واقع تلفیقی از ریخته گری و آهنگری است. مذاب با دمای مشخصی وارد قالب میشود و تحت فشار یک جک هیدرولیک شکل آن کامل میشود.
انواع کوره ریخته گری کوبشی
روش مستقیم
این فرایند به وسیله تجهیزاتی انجام میشود که به فرآیند فورج شباهت زیادی دارند. فلز مایع به قسمت پایینی قالب ریخته میشود و توسط یک فشار هیدرولیک منجمد میگردد. در این روش فشاری بسیار بالا در حدود ۱۰۰ مگاپاسکال و یا بیشتر به کل مذاب اعمال میشود تا زمانی که کاملا منجمد شود.
روش غیر مستقیم
این فرآیند بسیار شبیه به دایکست است و با تجهیزات این روش انجام میگیرد. ریخته گری کوبشی غیر مستقیم میتواند به صورت عمودی یا افقی انجام گیرد. به این صورت که مواد مذاب به شات اسلیو عمودی یا افقی ریخته میشود.
سپس مذاب از طریق دروازههای نسبتا بزرگ به درون قالب تزریق میشود. این کار با سرعتی آهسته (کمتر از ۰.۵ متر بر ثانیه) انجام میشود و پس از آن، مذاب با فشاری در حدود ۵۵ تا ۳۰۰ مگاپاسکال منجمد میشود. قطعات تولید شده با این روش در نهایت استحکام کششی مناسبی خواهند داشت.
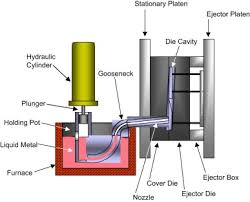
تفاوتهای بین کوره ریخته گری دقیق و کوره ریخته گری ماسه ای
هزینه: فرآیند کوره ریخته گری دقیق همیشه پر هزینه تر از کوره ریخته گری ماسه ای است چرا که پیچیدگی و آماده سازی بیشتری نیاز دارد.
وزن: در کوره ریخته گری دقیق می توان قطعاتی کمتر از 450 گرم تولید کرد. در حالی که در کوره ریخته گری ماسه ای نمیتوان همیشه قطعات کوچک و پیچیده تولید کرد. البته کوره ریخته گری دقیق هم محدودیت هایی در اندازه و وزن قطعات نیز با خود دارد. تجهیزات جا به جایی قالب در کارخانه کوره ریخته گری وزن قطعات تولیدی را تحت تاثیر قرار میدهد.
صافی سطح: صافی سطح یک تفاوت بزرگ دیگر بین این دو نوع فرآیند محسوب می شود.کوره ریخته گری دقیق میتواند قطعاتی با صافی سطح بالا و تلورانس پایین ایجاد کند. پس از جدا کردن راهگاه و فرآیند شات بلاست، قطعه نهایی آماده برای تحویل است. اما در ریخته گری ماسه ای، قالب باید از هم جدا شود تا محصول نهایی بدست آید.
در نتیجه، خط جدایش روی سطح خارجی قطعه نهایی باقی خواهد ماند. و به خاطر شن زبر، سطح قطعات نهایی نیز به همان اندازه خشن خواهند بود. بنابراین هزینه و زمان بسیاری صرف ماشینکاری ثانویه شده تا خط جدایش پاک گردد و صافی سطح بیشتری به دست آید.
سهولت طراحی: در کوره ریخته گری دقیق، قالب سرامیکی با استفاده از دوغاب مایع شکل میگیرد، بنابراین قطعات این روش را می توان تقریبا به هر شکلی ساخت، که به مهندسان آزادی فوقالعادهای در طراحیهای خود برای اضافه کردن اشکال پیچیده میدهد. در کوره ریخته گری ماسه ای، برای آن که قطعه از ماسه به آسانی با اصطکاک کمتری بیرون بیاید، قالب ها باید دارای شیب و زاویه خروج از قالب باشند.
همچنین برای کوره ریخته گری ماسه یکی از چالش ها، ساختی قطعات با حفره های داخلی است. در کوره ریخته گری ماسه ای به هسته هایی با شکل مناسب نیاز است تا در قالب وارد شود و فضای داخلی قطعه را تشکیل دهد. گاهی ممکن است چندین هسته مورد نیاز باشد، و همچنین زمان لازم برای تشکیل و ایمن کردن آنها در هر قالب را بایستی در نظر گرفت.
سلام قیمت کوره ریخته گری چند است توی بازار ؟؟
سلام دوست عزیز، برای اگاه شدن قیمت کوره ریخته گری یا قیمت کوره دایکاست داخل سایت b2wall شده از طریق رایچت یا تماس با پشتیبان های فروش در ارتباط باشید.
سلام سوالی برام پیش اومده آیا کوره ریخته گری همان کوره دایکاست برای تولید قالب ها است؟؟
سلام بله. کوره ریخته گری همان کوره دایکاست برای تولید قالب ها است.