تاریخچه دستگاه دایکاست در قرن 19
تاریخچه دایکاست
در این مقاله به تاریخچه دستگاه دایکاست می پردازیم :
انواع روش ریخته گری:
از پرکاربردترین روش های ریخته گری ساخت قطعات فلزی میتوان روش دایکاست یا ریخته گری تحت فشار را نام برد ، ریخته گری ثقلی در قالب ریژه، ریخته گری ماسه ای و ریخته گری دقیق هم به دنبال آن از مهم ترین و پرکاربرد ترین روش هاست. البته امکان اجرای فرایند ریخته گری به روشهای دیگری نظیر ریخته گری کم فشار، ریخته گری گریز از مرکز، ریخته گری لاست فوم ، ریخته گری کوبشی، ریخته گری تحت خلا و ریخته گری پیوسته هم وجود دارد.
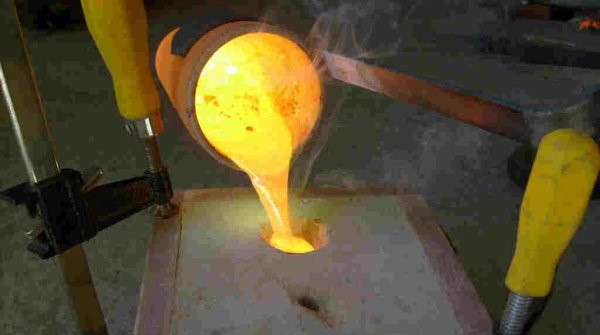
از متداولترین و قدیمیترین روشهای ساخت و تولید قطعات فلزی ریخته گری یا عمل دایکاست (die casting) توسط قالب ماسه ای است.
دایکاست یا ریخته گری تحت فشار :
ریخته گری تحت فشار یا دایکاست، از پرکاربردترین روشهای تولید انبوه قطعات فلزی پیچیده در صنایع مختلف است. تولید قطعات فلزی به روش دایکاست، از اصول مهم و کلی ریخته گری پیروی میکند. این روش طی فرایند ذوب، تزریق وانجماد انجام می شود.
ریخته گری تحت فشار ( دایکاست ) در تولید قطعات ساده تا پیچیده در صنایع مختلف مثل خودروسازی، جواهرسازی ، ساخت ماشینآلات صنعتی، هوافضا ، مجسمهسازی و… کاربرد بسیار دارد.
تاریخچه دستگاه دایکاست چیست ؟
در اوایل قرن 13 شمسی (که مصادف با اواسط قرن 19 میلادی می باشد) ، قابلیتهای صنعت چاپ با پیشرفت و توسعه زیادی همراه شد. اختراع تجهیزات ریخته گری تحت فشار (دایکاست) ، یکی از عوامل موثر بر رشد این صنعت بود. در آن دوران، ماشینهای تحریر از قطعات زیادی برای تایپ حروف، علائم نگارشی و اعداد تشکیل میشدند. فرآیند دایکاست، سرعت ساخت این قطعات و کیفیت آنها را از نظر یکنواختی ابعاد به میزان قابل توجهی افزایش داد.
این فرایند پیشرفته، کاهش تعداد خطاهای تولید و افزایش سرعت سرهم کردن قطعات را در پی داشت. کاربرد موفقیت آمیز ریخته گری تحت فشار یا فرایند دایکاست در صنعت چاپ باعث جلب توجه صنایع دیگر به این روش نوین شد.
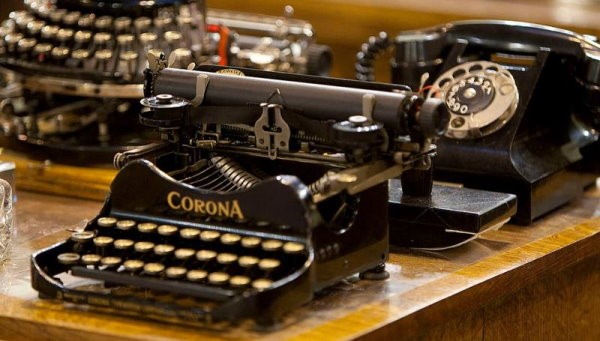
تولید اکثر قطعات ماشینهای تحریر به روش ریخته گری تحت فشار انجام می شود.
اولین تجهیزات مورد استفاده برای اجرای ریخته گری تحت فشار، دستگاه کوچکی بود که به صورت دستی کار می کرد. این دستگاه در سال 1838 میلادی و یا 1217شمسی اختراع شد و فرایند ریخته گری توسط این دستگاه دایکاست، با ذوب کردن ترکیبی از سرب و قلع و ریختن آلیاژ داغ و مذاب به درون یک قالب فولادی انجام می گرفت. قالب که در این فرآیند استفاده می شد با عنوان دای (Die) شناخته میشد. پس از سرد شدن و انجماد آلیاژ، قطعه ای به شکل حفره قالب به دست می آمد. به قطعه حاصل از این فرایند، کَستینگ (Casting) می گفتند.
به همین دلیل، به فرایند ریخته گری تحت فشار دای کستینگ (Die Casting) شناخته می شود که کارشناسان و صنعتگران فارسی زبان از اصطلاح دایکاست استفاده می کنند.
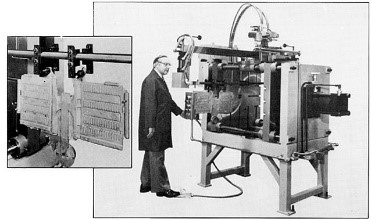
ریخته گری به روش دایکاست به مدت 30 سال فقط در صنعت چاپ مورد استفاده قرار گرفت. تا اینکه در اوایل دهه 1890 میلادی و اوایل دهه 1270 شمسی، صنایع کوچک و بزرگ دیگر هم به استفاده از این روش ساخت و تولید روی آوردند. به طوری که قطعات ماشین آلات صنعتی نیز به روش دایکاست تهیه میشدند.
در سال 1914 میلادی یا1293 شمسی، آلیاژ روی و آلومینیوم برای ساخت قطعات مقاومتر مورد استفاده قرار گرفت. چندین سال بعد، آلیاژهای مس و منیزیم نیز به فهرست مواد قابل استفاده در ریخته گری تحت فشار اضافه شدند. امروزه، دستگاههای دایکاست میتوانند قطعات متنوعی را از نظر شکل و خواص مکانیکی تولید کنند.
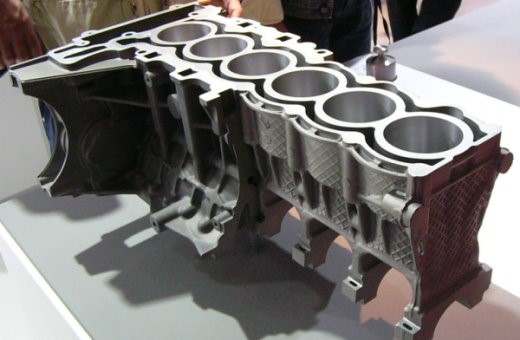
ریخته گری تحت فشار ساخته میشود
در سالهای اولیه معرفی دستگاه دایکاست، اجرای این فرآیند با محدودیت فشار قابل اعمال به مواد مذاب همراه بود. در واقع، سیستم تزریق مواد مذاب در فشار پایین انجام میشد.
پیشرفت ماشینآلات و افزایش مقاومت آنها در برابر فشار و دما، زمینه توسعه روش دایکاست و اجرای تزریق تحت فشار بالا را فراهم کرد. امروزه ریخته گری با فشار بالا به عنوان یک روش استاندارد و با کیفیت شناخته میشود.
یکی از کارآمدترین روشهای ساخت قطعات با شکلهای پیچیده، ساختار یکپارچه، ابعاد دقیق، سطح با کیفیت، مقاومت بالا و سختی مناسب ریخته گری تحت فشاراست.
به همین دلیل این روش کاربرد زیادی در تولید قطعات و تجهیزات صنعتی و کالاهای مصرفی، به خصوص قطعات اتومبیل دارد(حدود 60 درصد از قطعات ساخته شده به روش ریخته گری دایکاست در صنعت اتومبیلسازی مورد استفاده قرار میگیرند). در صنایع هوافضا، تجهیزات الکترونیکی، ساخت لوازم خانگی و جواهرسازی نیزاین روش کاربرد دارد.
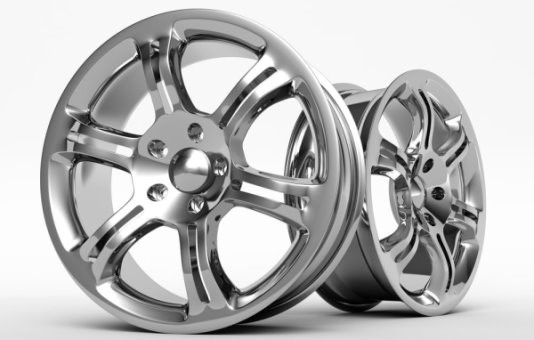
چرخ و چراغ دایکاست مانند چراغهای شهری و لوستر دایکاست، ظروف دایکاست مانند قابلمه دایکاست، رادیاتور دایکاست و…از مواردی هستند که توسط این روش ساخته میشوند.
تاریخچه ساخت قالب دستگاه دایکاست
به محفظه های فلزی با قابلیت استفاده مجدد dies میگویند که در تولید قطعات صنعتی پیچیده استفاده میشود. در این قالب سازی صنعتی معمولاً یک آلیاژ غیر آهنی مثل آلومینیوم یا روی، در کوره ذوب شده و سپس به محفظه در دستگاه ریختهگری تزریق میشود.
این صنعت به اواسط قرن 19 در ایالاتمتحده باز میگردد که در آن یک فلز مذاب یا آلیاژ، با فشار بالا به یک محفظه فلزی تزریق میشود. هنگامی که فلز تزریقی جامد شد، محفظه باز میشود و قطعهای از آلومینیوم ریختهگری استخراج میشود.
امروزه ساخت دستگاه دایکاست جدید بدین صورت است که قطعاتی از جنس آلومینیوم که دارای ضخامت یکنواخت بین ۱٫۵ تا ۱۵ میلیمتر هستند از روش ریختهگری تحت فشار ساخته می شوند. دستگاه دایکاست در این روش مذاب آلومینیوم با فشار بالا داخل قالب تزریق میشود. از مزیت های ساخت دستگاه دایکاست تولید قطعات با کیفیت سطحی بالا و تیراژ است.
کیفیت بالا و عدم پلیسه باعث میشود بسیاری از پروسههای تولید مانند پلیسه گیری و سنگ زنی و سوراخ کاری حذف شود، از این رو تأثیر به سزایی در کاهش هزینه تولید هر واحد قطعه دارد.
دستگاه دایکاستی که در این روش مورد نیاز است، از جنس فولاد گرمکار با حجم و ضخامتی زیاد است. این محفظه ها قابلیت تحمل فشار بالای ذوب را دارند، از این رو die cast محفظه هایی گران قیمت و بزرگ هستند.
جهت مشاهده محصولات قابل تولید با دستگاه دایکاست کلیک کنید.
سلام ریخته گری تحت فشار یعنی چه؟؟
سلام ریخته گری تحت فشار همان دستگاه دایکاست به صورت تحت فشار ، قالب ها تولید می شوند.
سلام قالب ها با دستگاه دایکاست ساخته می شود؟؟
سلام بله قالب ها با دستگاه های دایکاست ساخته می شود.
انواع روش ریخته گری کدامند؟
ریخته گری کم فشار، ریخته گری گریز از مرکز، ریخته گری لاست فوم ، ریخته گری کوبشی، ریخته گری تحت خلا و ریخته گری پیوسته
ریخته گری تحت فشار در چه کارهایی کاربرد دارد؟
ریخته گری تحت فشار ( دایکاست ) در تولید قطعات ساده تا پیچیده در صنایع مختلف مثل خودروسازی، جواهرسازی ، ساخت ماشینآلات صنعتی، هوافضا ، مجسمهسازی و… کاربرد بسیار دارد.
مزیت استفاده از دستگاه دایکاست در قرن 19 چه بود؟
در آن دوران، ماشینهای تحریر از قطعات زیادی برای تایپ حروف، علائم نگارشی و اعداد تشکیل میشدند. فرآیند دایکاست، سرعت ساخت این قطعات و کیفیت آنها را از نظر یکنواختی ابعاد به میزان قابل توجهی افزایش داد.
پیشرفت دستگاه دایکاست در چه سال و چه زمینه ای بود؟
ریخته گری به روش دایکاست به مدت 30 سال فقط در صنعت چاپ مورد استفاده قرار گرفت. تا اینکه در اوایل دهه 1890 میلادی و اوایل دهه 1270 شمسی، صنایع کوچک و بزرگ دیگر هم به استفاده از این روش ساخت و تولید روی آوردند. به طوری که قطعات ماشین آلات صنعتی نیز به روش دایکاست تهیه میشدند.
زمینه توسعه دستگاه دایکاست چجوری فراهم شد؟
پیشرفت ماشینآلات و افزایش مقاومت آنها در برابر فشار و دما، زمینه توسعه روش دایکاست و اجرای تزریق تحت فشار بالا را فراهم کرد. امروزه ریخته گری با فشار بالا به عنوان یک روش استاندارد و با کیفیت شناخته میشود.
dies چیست؟
به محفظه های فلزی با قابلیت استفاده مجدد dies میگویند که در تولید قطعات صنعتی پیچیده استفاده میشود. در این قالب سازی صنعتی معمولاً یک آلیاژ غیر آهنی مثل آلومینیوم یا روی، در کوره ذوب شده و سپس به محفظه در دستگاه ریختهگری تزریق میشود.
امروزه ساخت دستگاه دایکاست چگونه است؟
امروزه ساخت دستگاه دایکاست جدید بدین صورت است که قطعاتی از جنس آلومینیوم که دارای ضخامت یکنواخت بین ۱٫۵ تا ۱۵ میلیمتر هستند از روش ریختهگری تحت فشار ساخته می شوند. دستگاه دایکاست در این روش مذاب آلومینیوم با فشار بالا داخل قالب تزریق میشود. از مزیت های ساخت دستگاه دایکاست تولید قطعات با کیفیت سطحی بالا و تیراژ است.
شرایط ثبت سفارش دستگاه دایکاست چگونه است؟
سلام b2wall را در گوگل سرچ کرده و از قسمت درخواست قیمت مشخصات خودرا ثبت کنید تا مشاوران با شما تماس بگیرند